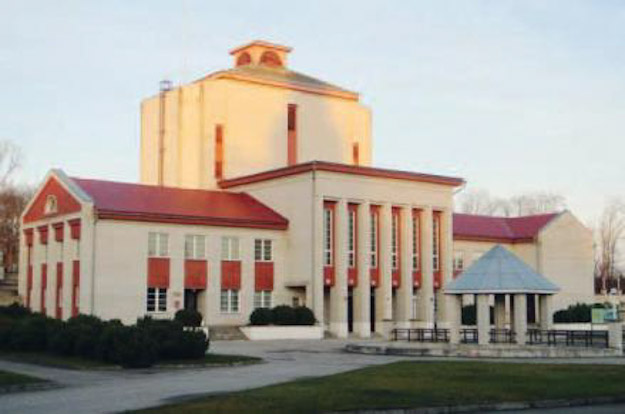 Lihula is a town in Estonia with 1600 inhabitants. Although the town is really small, it has a culture house with a 420 seat cinema. Movies are showed twice a month.
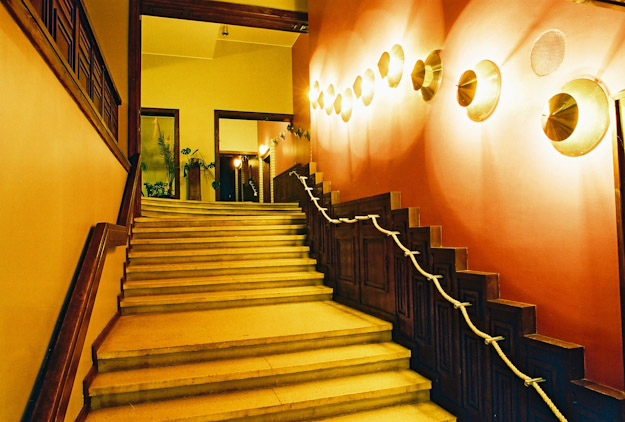 The main hallway to the auditorium.
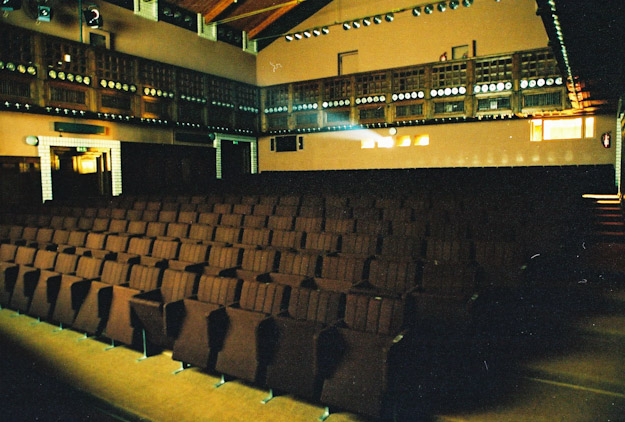 The auditorium as viewed from the front.
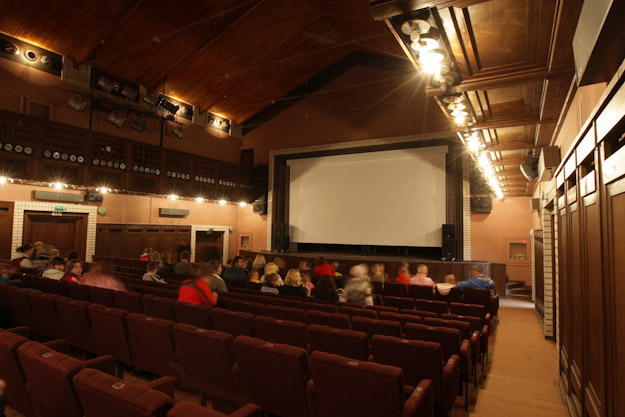 The auditorium as viewed from the rear. The screen is changed. The old screen was much smaller.
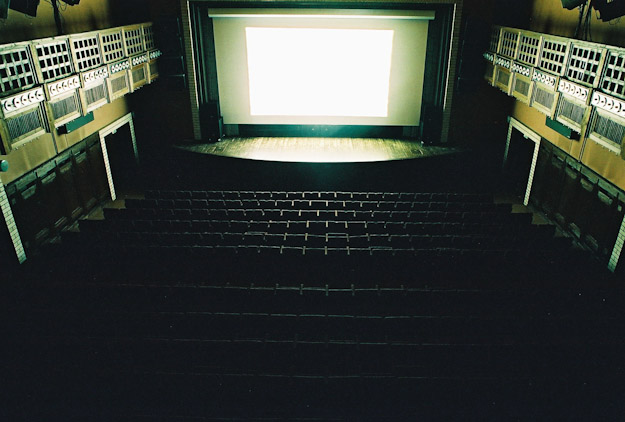 The auditorium as viewed from the balcony. The bad thing with this screen is that the flat lens is too long to fill the screen. There is a 75mm (3 inch.) lens right now, but it should be 65mm (2.5 inch). According to the old books the Soviets also made 65mm lenses, but no-one has never seen them. 65mm lens was the widest made in Soviet Union. Schneider or ISCO lenses are too expensive for a small cinema.
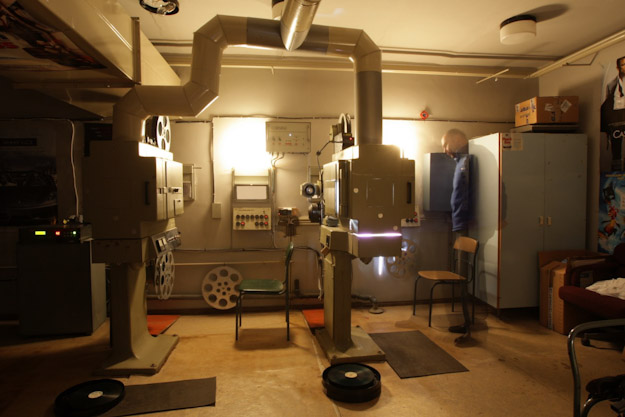 The projection room with a ghost-projectionist.
 Projectors are 400kg heavy LOMO 23KPK - these projectors were probably built in larger quantities than any other projector in the world. Most Soviet projection booths were fitted with these machines. According to the Russian forums these projectors were also produced under the license in China. The history of these projectors goes back to 1930s. The lamphouses were modified but the projectors head remained basically unchanged for 60 years. The production ended in 1993. A lot of cinemas in Estonia have been closed down and one can buy a set of 23KPKs for about 500 dollars or even less. A lot of almost brand new projectors have been sold as scrap iron. These projectors in Lihula are produced in 1989 and they have only 300 hours on them together. Pretty good projectors if you beat them up yourselves. I have never ever seen one to fail, which I can't say about Highlight II and Simplex Apogee I'm using right now. The only bad thing about these old beasts is that they are extremely noisy like they were a modification of a lathe. I still show movies in my dreams with these projectors.
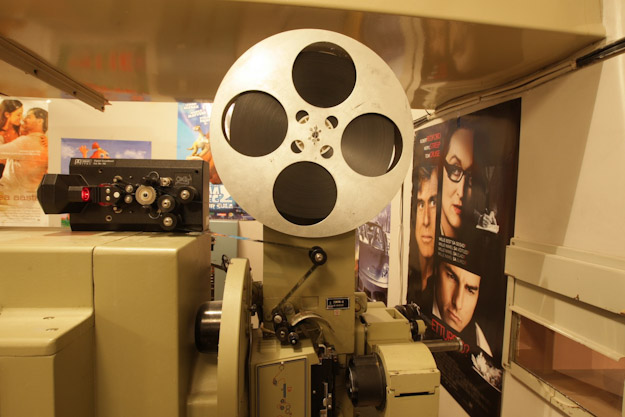 Have you ever seen something like this before? Dolby Digital reader placed on the lamphouse!
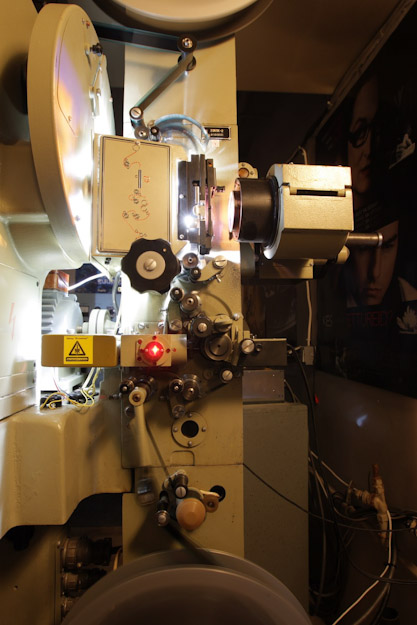 A closer look to the projectors head. Constantly lubricated gearbox, all gears are made from hardened steel. This projector will hold up almost forever. Although the threading path is very easy, I have seen projectors where the lower loop has constantly been too big and the paint has been worn off from the projector. Right before the take-up reel you can see the cue detector for automated changeover. But the movies here are showed only once, so the changeovers are done manually.
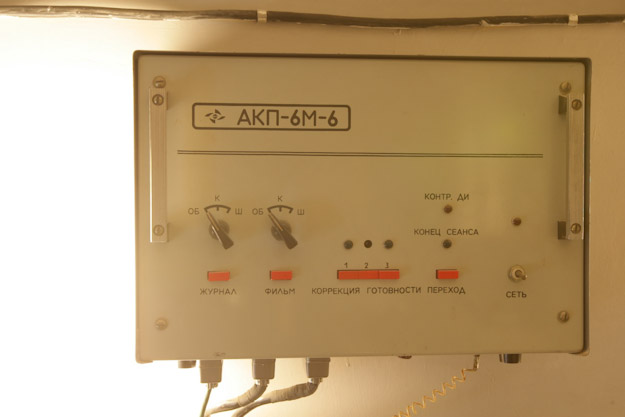 The automation.
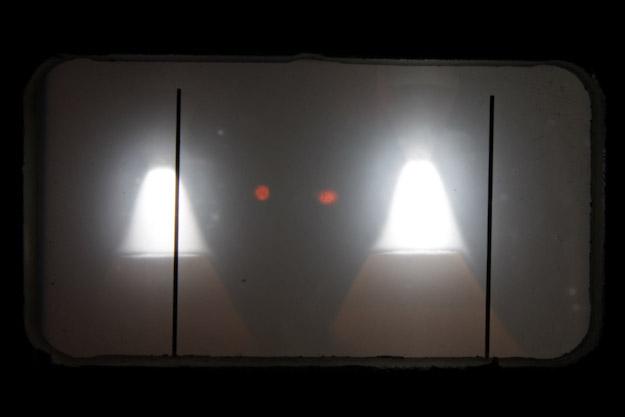 There is a small screen on the lamphouse, where the xenon arc is projected. It is used to focus the lamp. If you set the arc right on the black lines, the screen should be properly illuminated. But quality control in the factory has been poor and you get better results if you don't follow it.
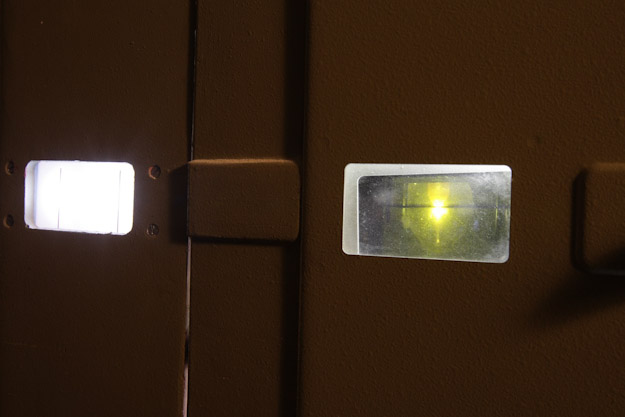 The lamphouse is vertical and and can run 2kW or 3kW bulbs. No-one has ever seen a 2kW bulb in these projectors before. When the motor is off, the current drops to 20 amperes and jumps back to 100 when the motor is started. Soviet 3kW bulbs have/had warranty for 1000 hours but they usually blew before. A colleague said that in Soviet time, when the stores were all empty, the old xenon bulb electrodes were used for welding. One more interesting thing: Soviet bulbs and reflectors were segregated into four classes depending on their color temperature, so you can adjust the color temperature on the screen. If the bulb was too blueish you had to use a "yellow" mirror. But very often the projectionists had no choice to select bulbs and reflectors, they had to use what was given to them. So it was usual that one projector had white picture while the other one was blue.
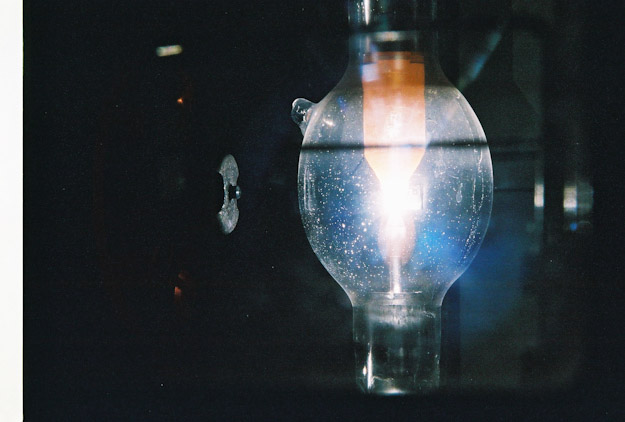 Closer look to the xenon bulb. Air bubbles in the quartz envelope? Hmmm...
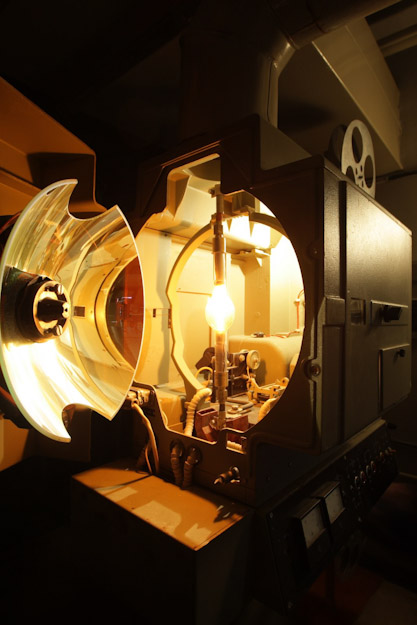 Opened lamphouse with xenon bulb still glowing. These lamphouses use AC ignitors. These lamphouses originally had a small reflector facing the big one. But these are removed, because the light output is much more higher without these small reflectors.
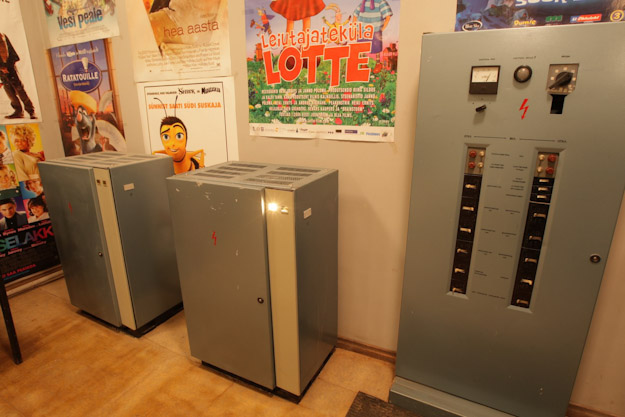 A heavy power supply. I remember how these beasts were clattering when the bulb striked and the amp meter was jumping between 20 and 150 amperes until the arc stabilized. I talked with a projectionist who worked here when these projectors were installed. It turned out that the Russian cinema technicians used aluminum wires instead of copper between the power supply and lamphouse! 100 amps running through thin aluminum wire? Wohooo!!! These wires were changed out immediately. I heard that the technicians were drunk most of the time. Back then the pure alcohol was given to all photographers, projectionists and technicians to keep the lenses clean. Pretty often the alcohol "was used to clean up the optical axis".
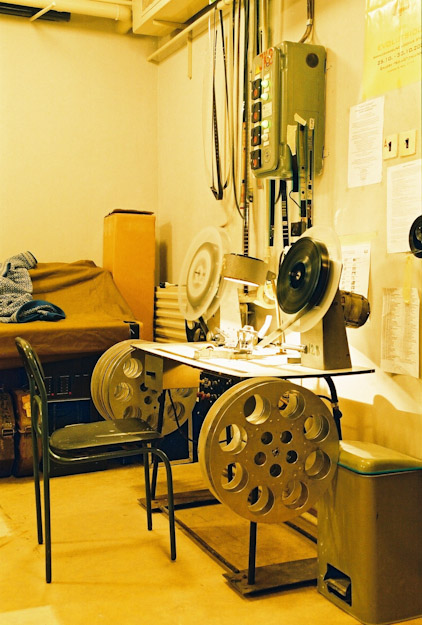 The rewind bench. A lot of leaders must be kept for spares because sometimes the projectionists who are working with platters don't splice the leaders back. Or, if they do, they don't tear the old splice, they just cut a new one right next to it. I have seen eight splices right after and before leaders! That's just sad.
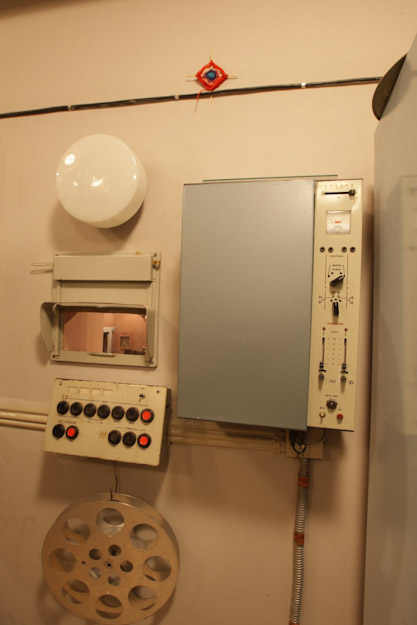 Old mono amplifier. It's not in use anymore.
|