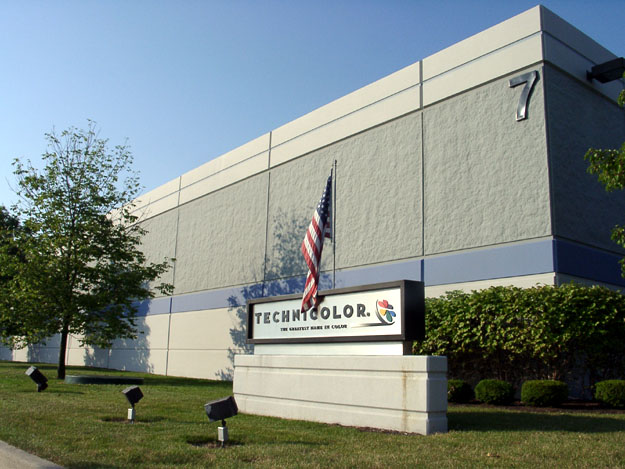 Here it is, the Technicolor facility in Wilmington Ohio!
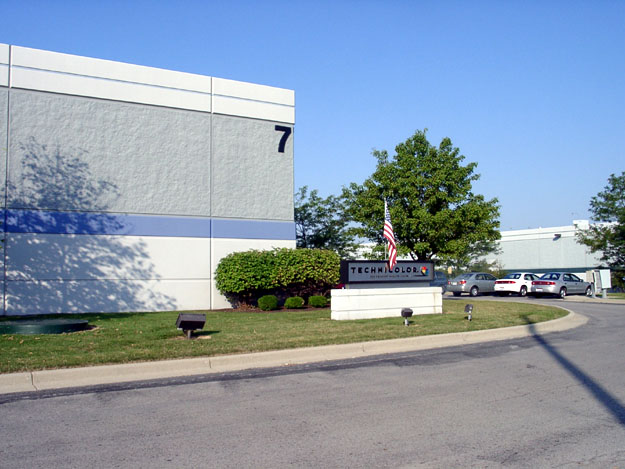 From the outside this place looks like an ordinary business complex.
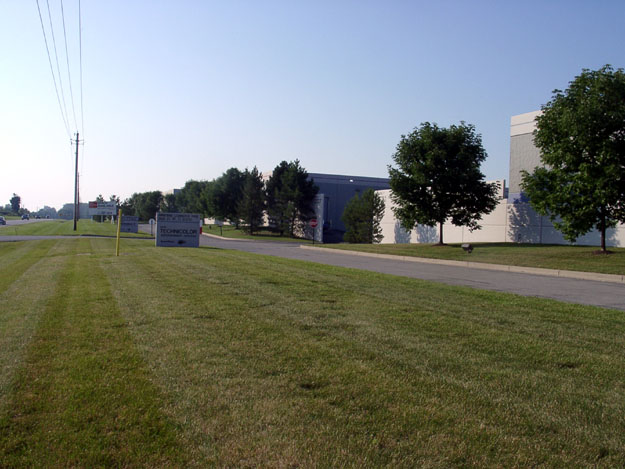 In fact it IS in a business park, but of course the surprising part is that the building is not painted orange.
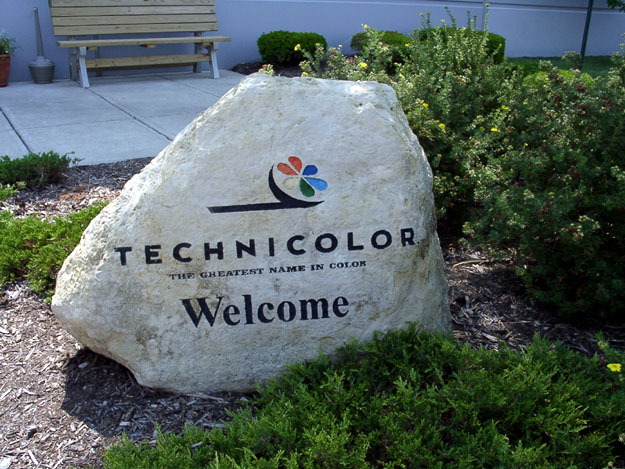 Just outside the main entrance is the "Technicolor rock".
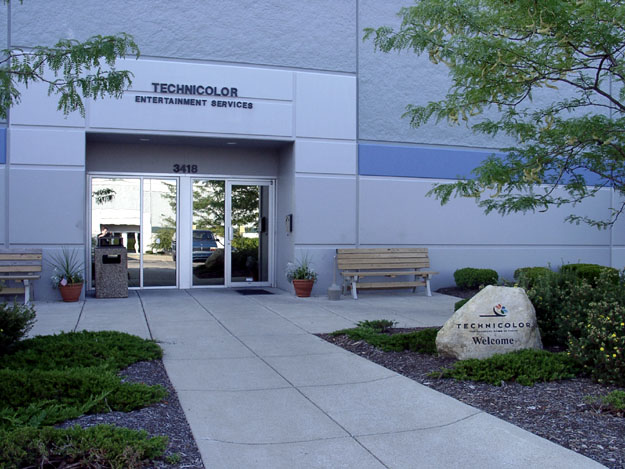 Are you ready to go inside?
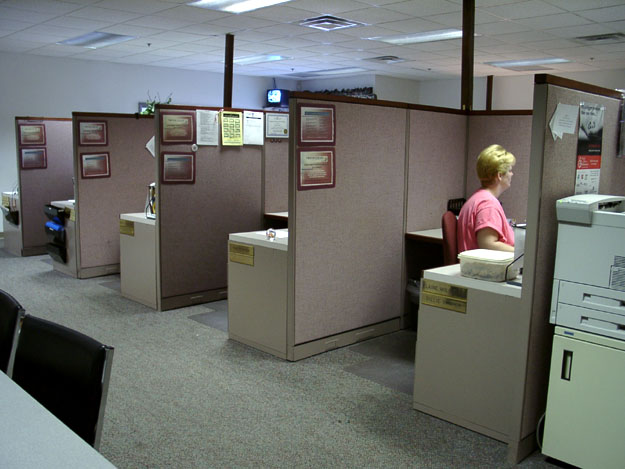 Here is the customer service department. This one room with 20 or so cubicles is where your calls are answered.
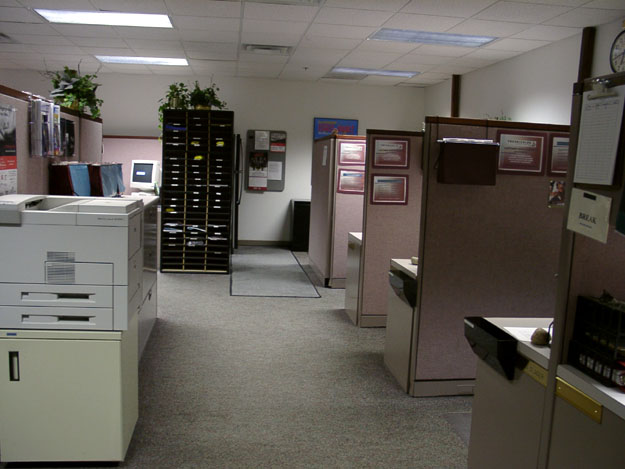 Another angle of the customer service department room.
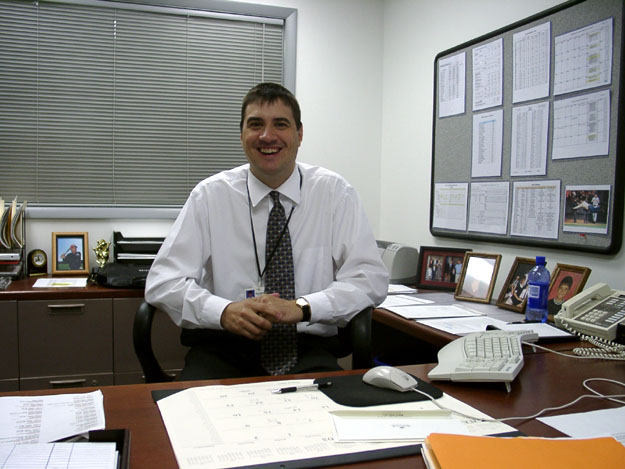 Let's meet a few people. This is Tony Butcher, the manager of print control.
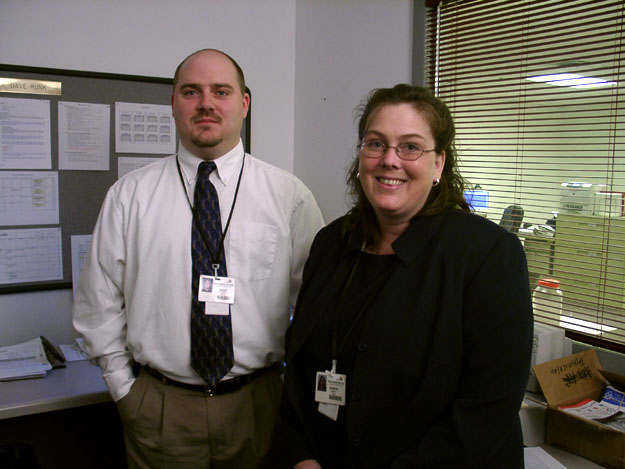 David Runk, manager of logistics and Robyn Long-Esmail, manager of screen services.
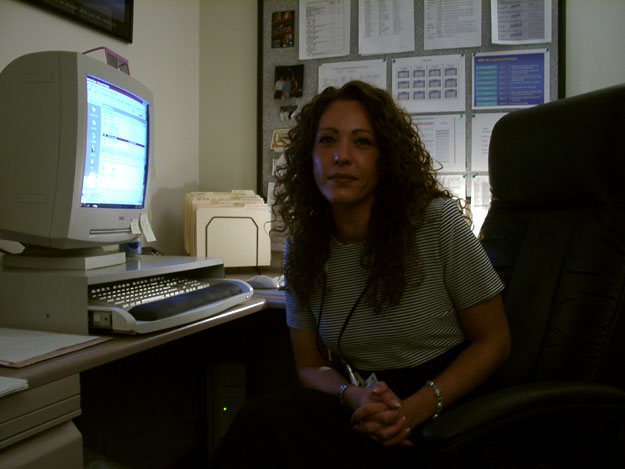 Stacey Downer, manager of inventory.
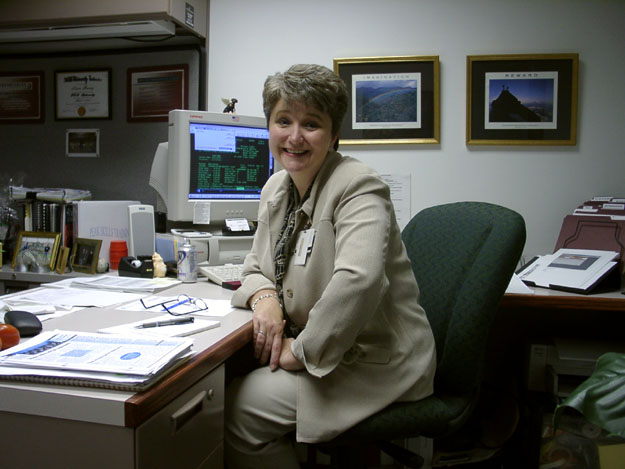 Sharon Benning, manager of customer service.
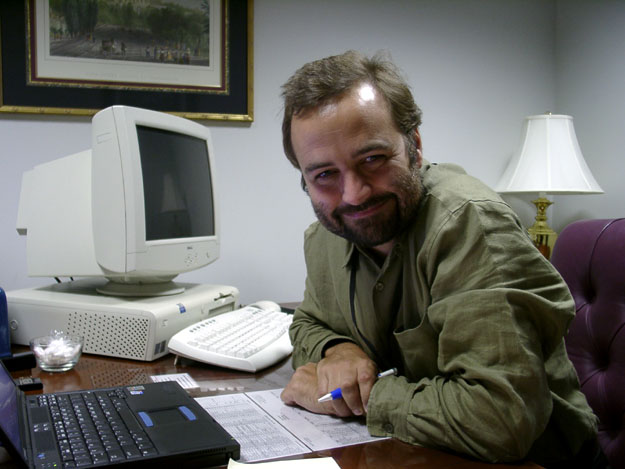 Brad Carroll, director of sales.
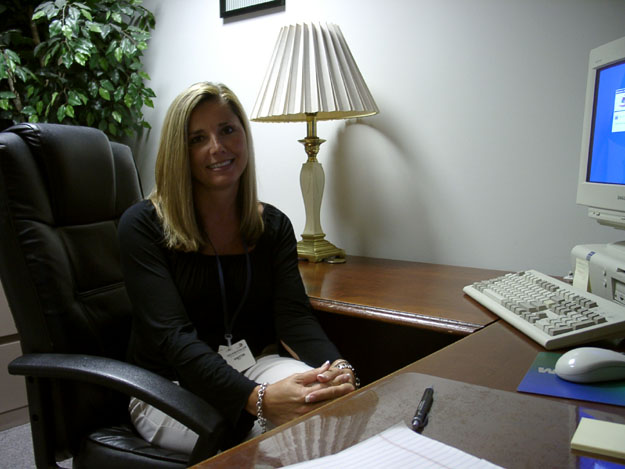 Lisa Ellers, manager of exhibitor relations.
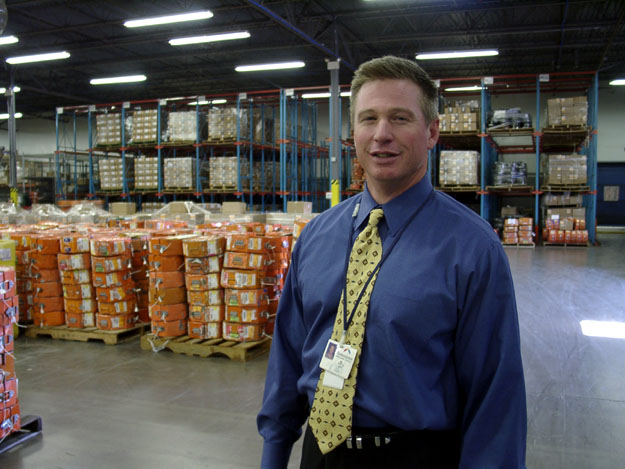 Al Barilar, operations manager.
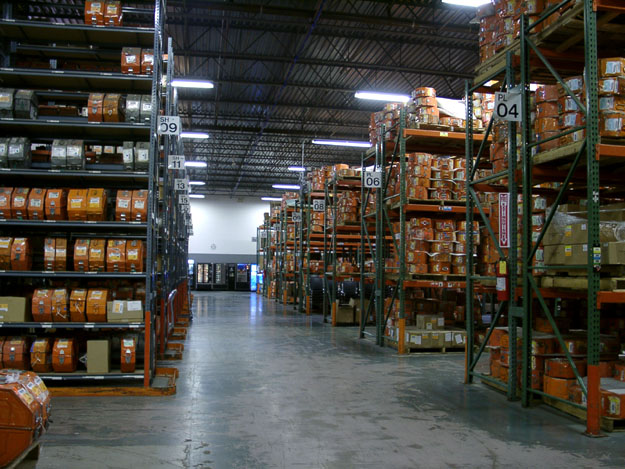 And here we are, one of the print storage warehouses. This particular warehouse is climate controlled for repertory print storage.
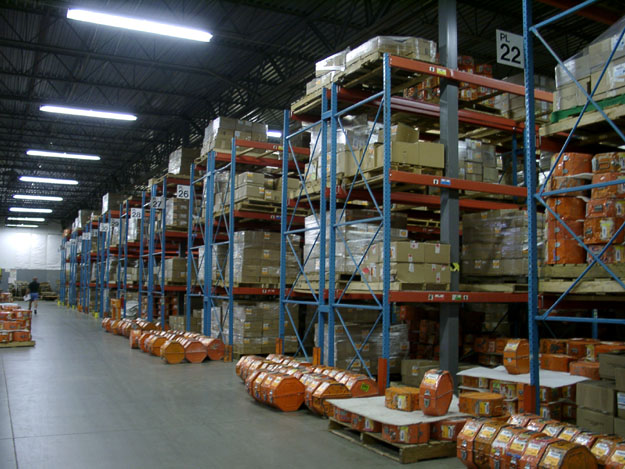 Here is more general storage. Notice how every row is numbered like a library. This is so every print has a specific storage spot and can be easily located and accounted for.
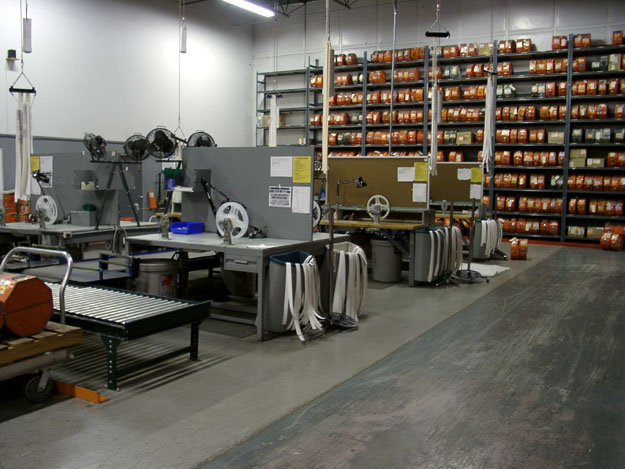 In one corner of the climate controlled storage are the integrity check stations. This is where all prints are spot-checked before they are shipped out to their next playdate.
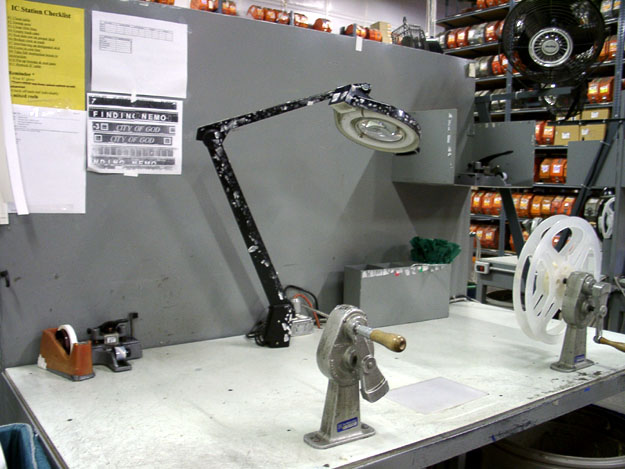 One of the integrity check tables.
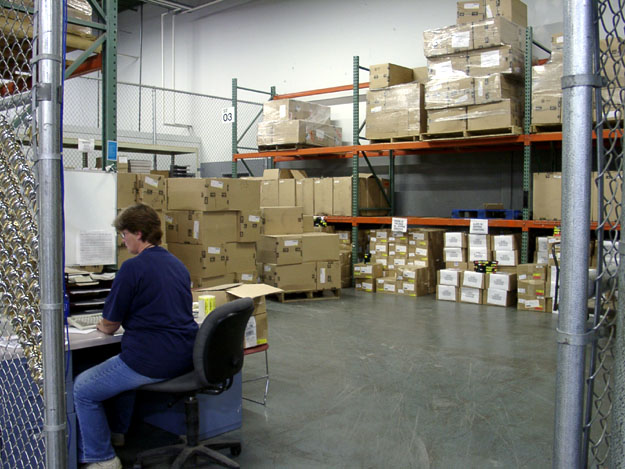 The next warehouse over has a couple of secure storage areas. In this area dts discs and some special prints are being stored.
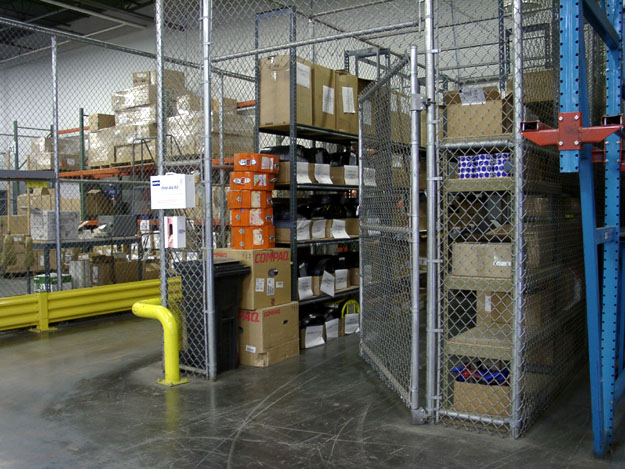 Another secure storage area.
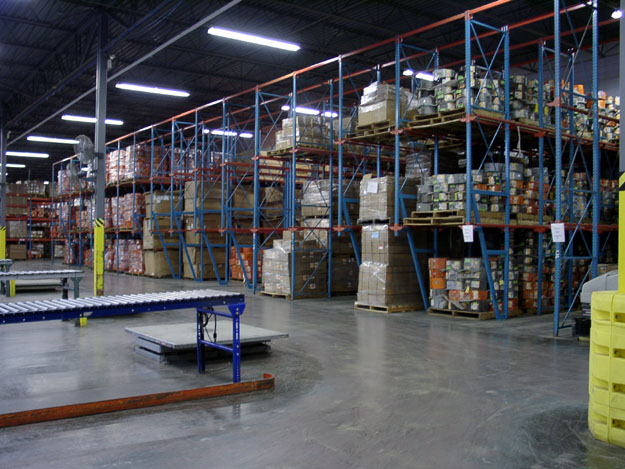 In the main shipping warehouse you will see on the left a few of the repack lines at their starting point.
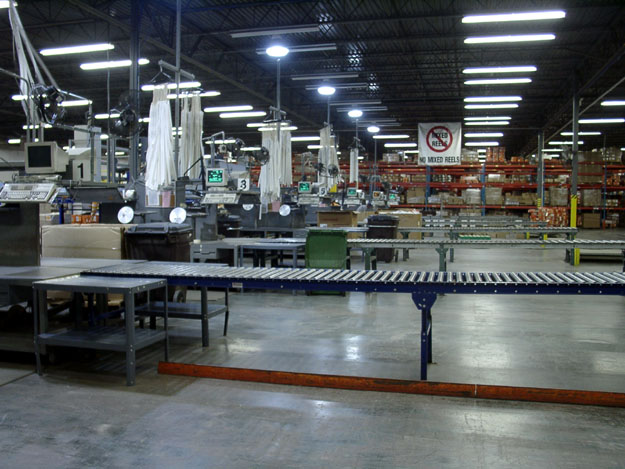 New prints from the lab are put on those assembly lines.
 Al Barilar invites us to watch how the prints are assembled.
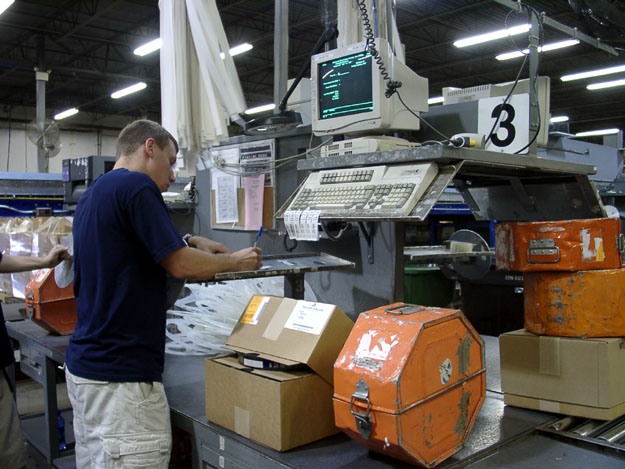 Each station is handled by two employees. Each one does 1 can of the movie (assuming 2 cans). After the necessary paperwork is done the original cardboard box from the lab is opened, two empty cans are prepped with the appropriate labels...
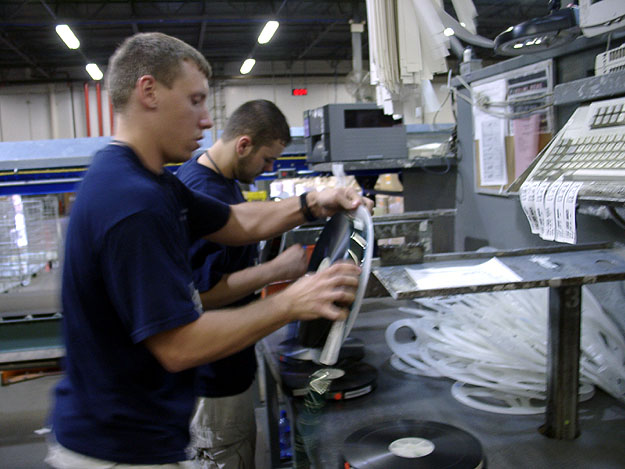 ...and they start mounting the cores of film onto clip together reels. During this time they unroll the first couple of feet of the leader to ensure that the printing lab did not make a mistake and pack two of the same reel or missed one. Also checked is to ensure the audio tracks are English.
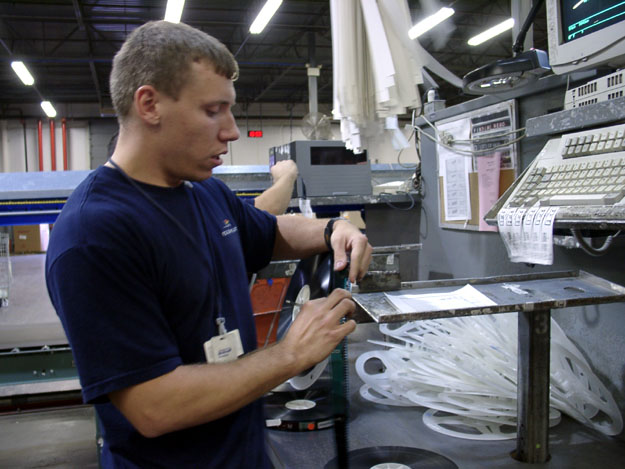 Once all of the reels are assembled and accounted for, trailers, dts discs and other loose items are placed in the cans and then it's time for the next print.
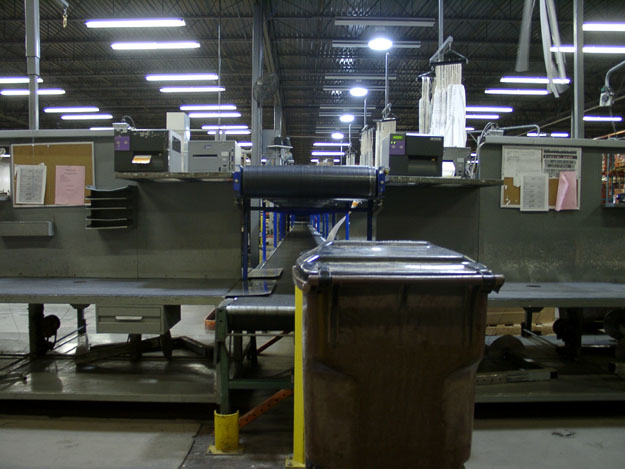 From there the cans ride down this assembly line. (There are print assembly stations on either side.)
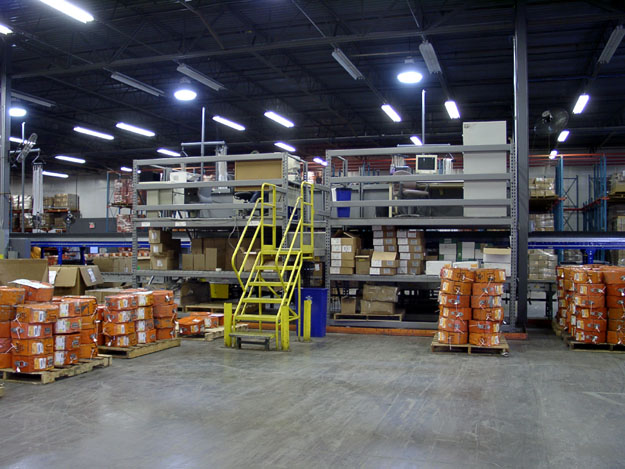 The supervisor station.
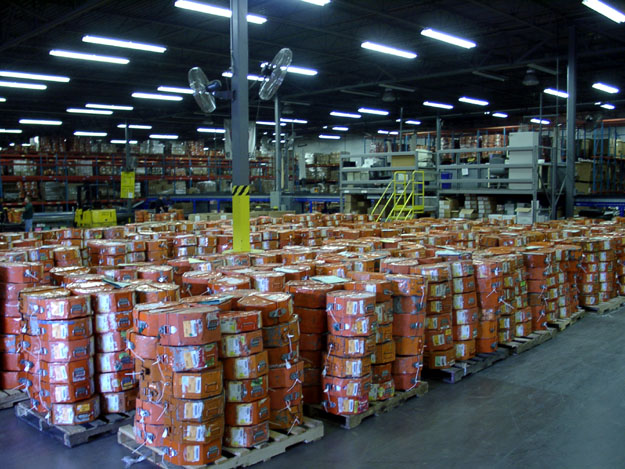 After a little time has passed, suddenly the area looks like this! Pictured here is close to 1000 prints of a new movie ready to ship to theaters.
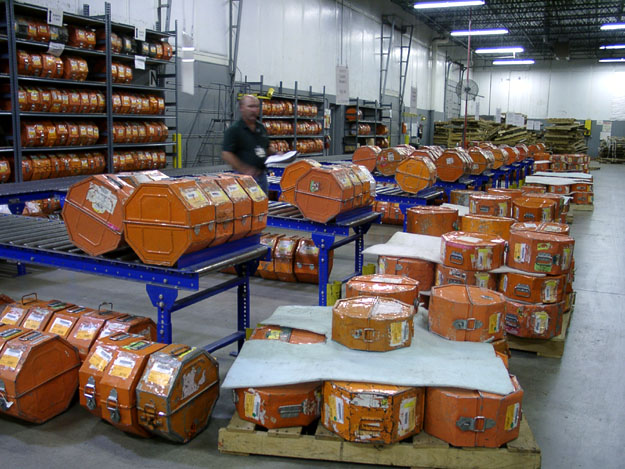 Pictured here are the assembly lines for print returns. To the left are several loading docks.
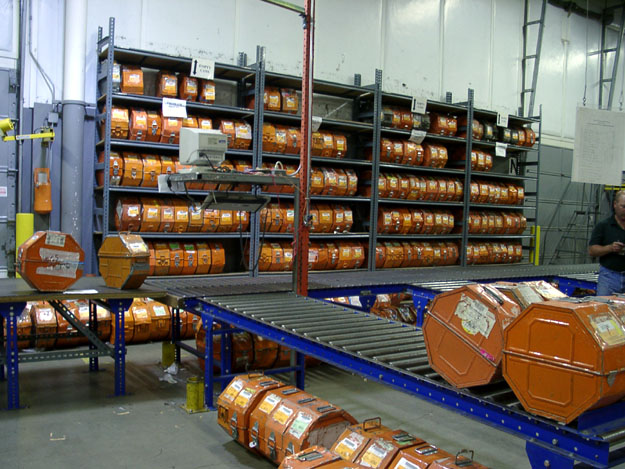 Another view of the print returns lines.
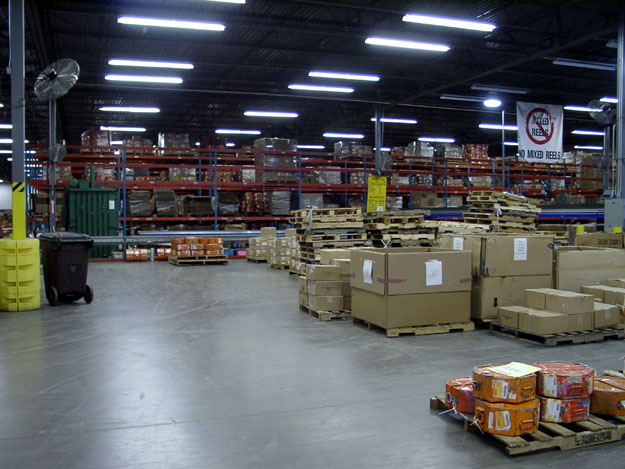 Staging area in the warehouse.
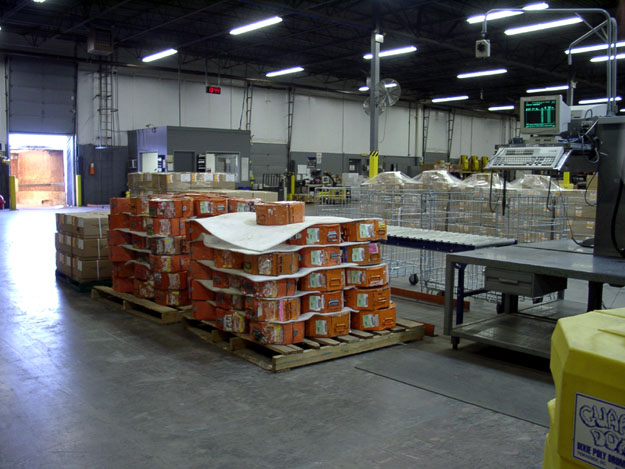 Several hours later that staging area looked like this. Trucks had delivered many skids of prints in boxes from the lab (seen on the right in the background), and many of those prints had already been converted onto reels and in cans ready to ship.
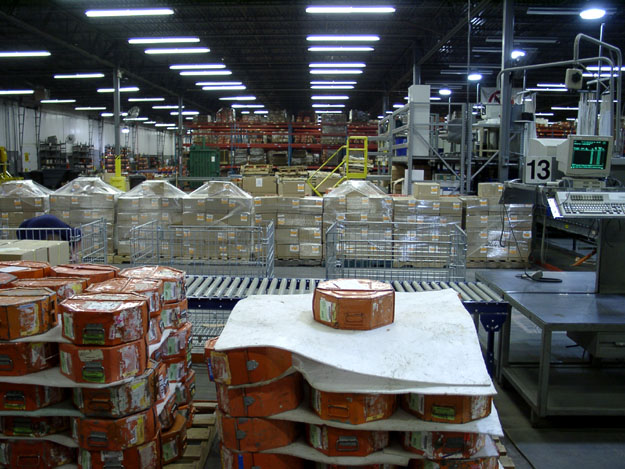 A better view of the previous picture showing many skids of prints awaiting conversion.
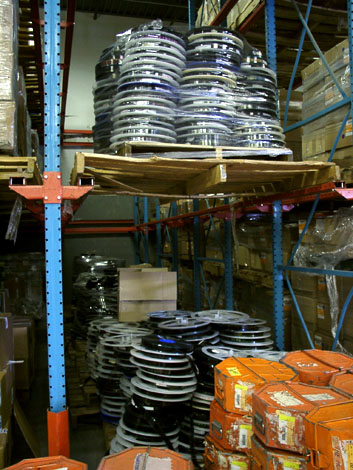 Here is a shot of some reject reels awaiting destruction.
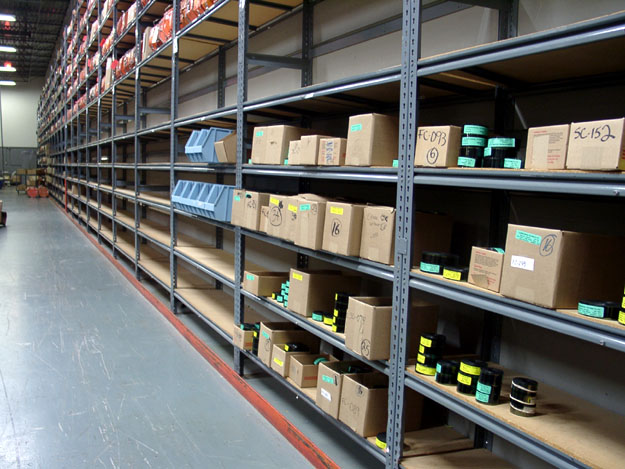 This is the storage area for Screen Services (rolling stock ads and public service announcement snipes).
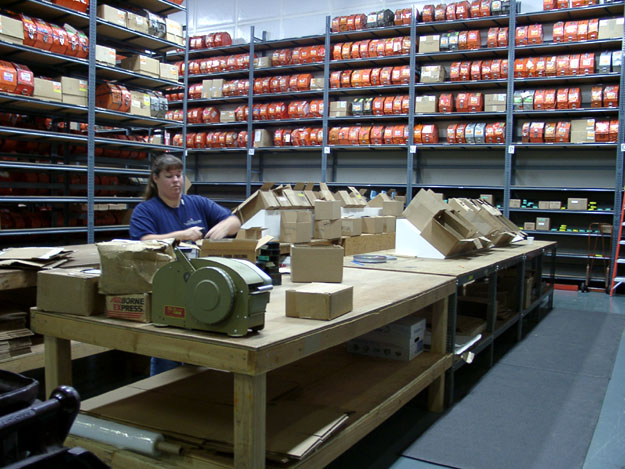 Pictured here is the Screen Services fulfillment area. A worker is seen organizing the necessary snipes for an upcoming shipment. (The upper shelves are more repertory prints being stored.)
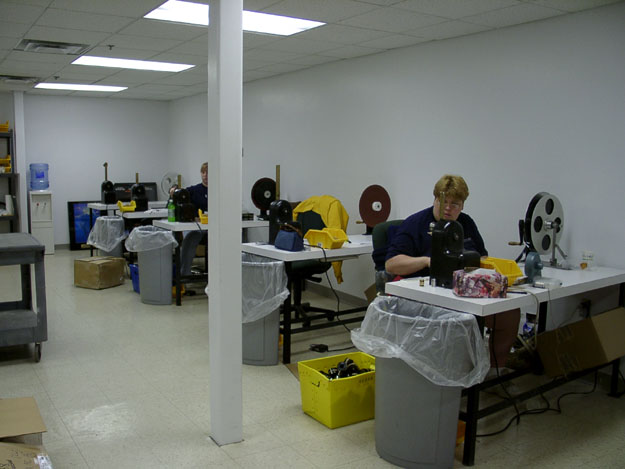 This room is where Screen Services winds off the snipes. The snipes are sent on normal size reels and spooled/cut into individual rolls here.
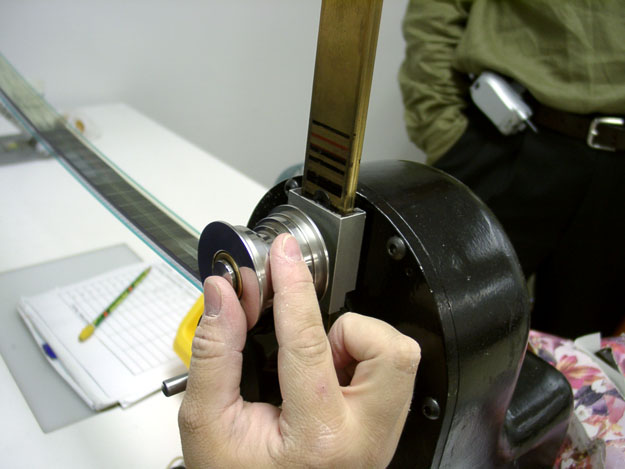 This is the tightwinder used to wind the snipes over to a "core-less" roll.
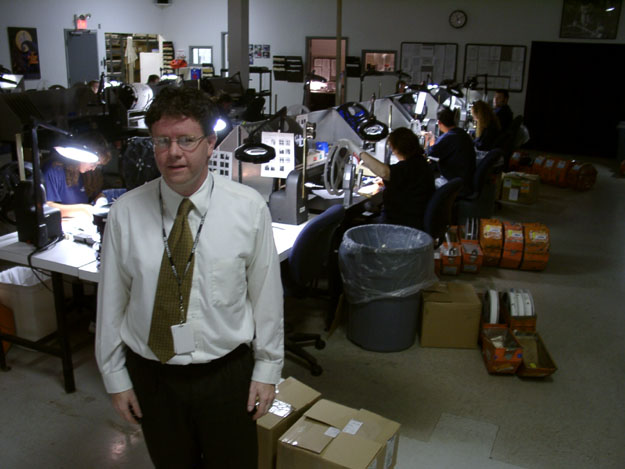 But shipping prints is not all that TES does. Meet Joe Wade, director of print services and Screen Services.
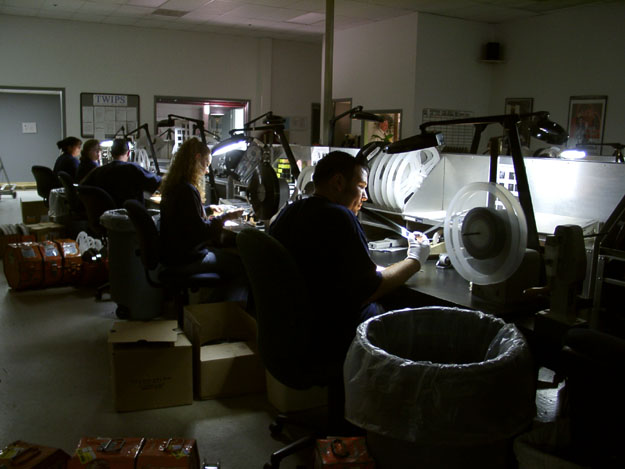 Joe oversees the "full" inspection team. In this room prints are fully inspected end to end. This is much different from the "quick check/integrity inspection" that most of theaters in the US are familiar with (which we saw in earlier pictures).
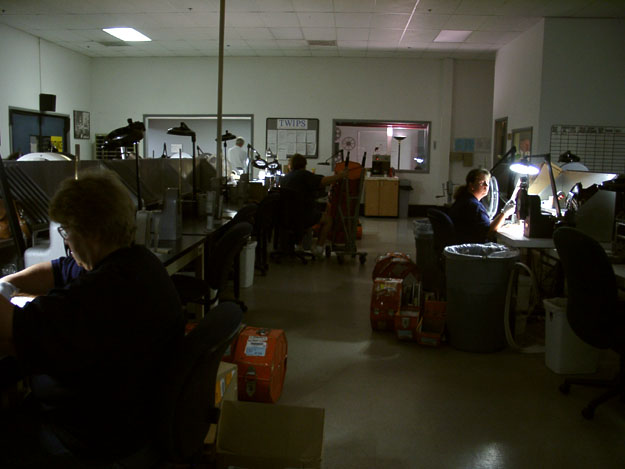 This part of the facility is used mainly for doing full inspections on "to be" repertory prints and for performing full inspections before the prints are rejuvenated and sent to overseas markets. (Just imagine what a mess it would be for someone in Europe to get a print with a 5 minute chunk missing out of it! Indeed, each reel is not only hand inspected, but ran through a frame counter and must conform to the original length of the reel with only a few frame error being acceptable.)
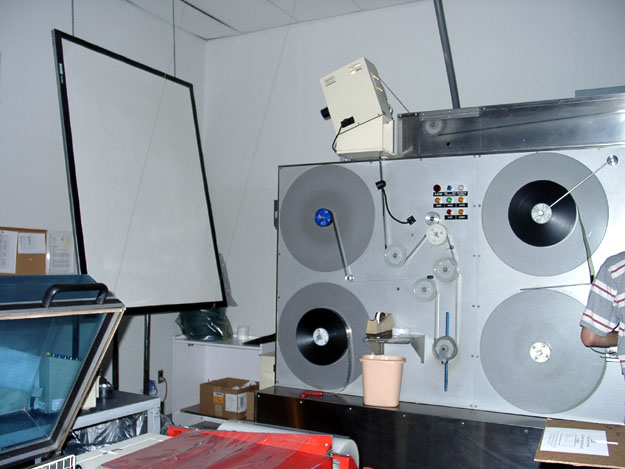 This is part of the cell treatment machine, sometimes known as "ImageGuard". We can't show you the rest of the machine off of the right side of this picture, as that would have been infringing on proprietary technology. What you CAN see here is the final winding onto cores as the film comes out of the treatment and it being projected onto this screen to verify the scratches do not project. (Note-this picture was taken with a flash so the image is not able to be seen.)
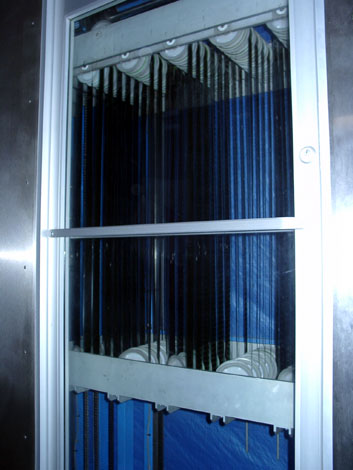 This is part of the rewashing process which pulls all dirt and other contamination off of the prints, as well as swelling the emulsion to fill in emulsion side scratches. Again virtually everything in this room was proprietary technology, so we were only able to show you this from the rewash room.
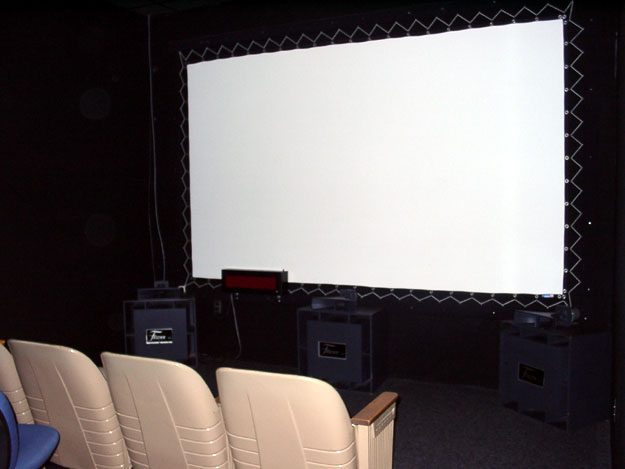 This is the TES screening room. It is not meant to be an actual place to sit and watch movies, but as a place to physically project a reel of film for inspection purposes. There is no aperture plate (just like on the individual viewers that we were unable to show you) to ensure that all of the image is being seen.
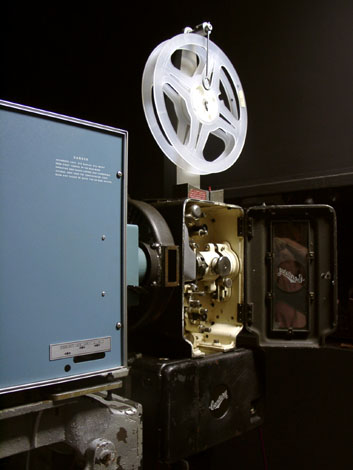 The projector for the screening room.
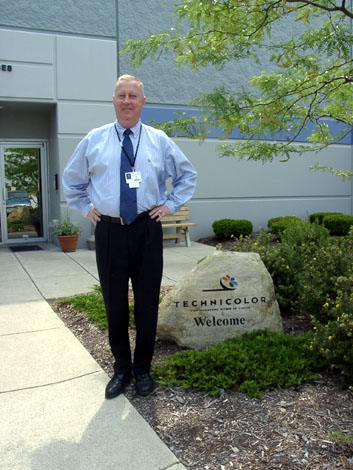 We close the tour with a HUGE thanks to Tim Burke, general manager of print management for Technicolor Entertainment Services. Tim was the primary push for us to be able to give everyone a "virtual tour" of the facility and is one who has been pushing for many recent improvements in their service.
Everyone say "thanks Tim!"
|