|
|
Author
|
Topic: Automated change over system for Simplex PR1014
|
|
Randy Stankey
Film God
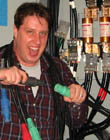
Posts: 6539
From: Erie, Pennsylvania
Registered: Jun 99
|
posted 02-23-2018 09:12 AM
It's absolutely doable but I don't remember any specific automation systems that do it but, really, many automation systems can probably be set up to do it.
If it was me, I'd make my own. All you need are some 555's (or similar), some opto-isolators, some relays and a few other random parts. It's not hard.
However... I'd do some thinking before you decide whether to go forward with such a project.
As I was brought up, the First Commandment of Projection is, "Thou shalt not start a projector without an operator standing by."
I don't care how trustworthy your machines are. I don't care how well-trained your operators are. I don't care how good you think you are. If a projector starts automatically there is ALWAYS the chance that something will go wrong and there won't be anybody within arm's reach to fix it.
That is how movies start up out of focus, out of frame or with bad sound.
That is how film gets scratched and damaged. That is how prints get trashed.
I have seen all of these things happen to people who let their projectors start on timers, etc.
All of these things have happened to me because I got cocky and thought I was too smart to let something like that happen. In reality, I was too smart for my own good.
In this day and age, with good, clean film prints getting harder to come by and with the people/companies who own them getting more and more circumspect about loaning/renting them out, my advice is to just learn how to make a good changeover by hand.
Learning how to make a changeover isn't very hard. It only takes a little bit of practice. Once you get the hang of it, you should be able to make frame-accurate changeovers almost by second nature.
Besides... Back in the day, making frame-accurate changeovers was an everyday occurrence but, today, it's something to brag about!
| IP: Logged
|
|
|
|
|
|
Brad Miller
Administrator
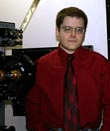
Posts: 17775
From: Plano, TX (36.2 miles NW of Rockwall)
Registered: May 99
|
posted 02-23-2018 04:00 PM
I know I'm in the minority on this, but I don't think even manual changeover booths should EVER run without at LEAST a film break failsafe on it to immediately shut the movie down. I've seen too many times over the years where a takeup belt would break, or a tear in the film would break after it exited the projector on route to the takeup reel...and a mountain of damaged film is left behind! Also IB tech prints in particular tend to have a good chance of an edge tear that tears to the center of the film and then continues to tear directly lengthwise down the ENTIRE rest of the reel (without interrupting projection)!
Check out these two photos of exactly this disaster...
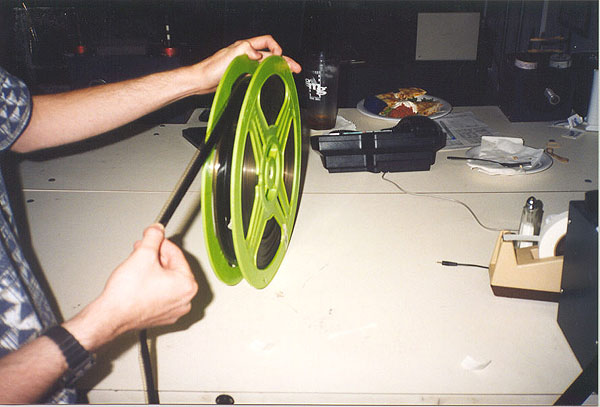
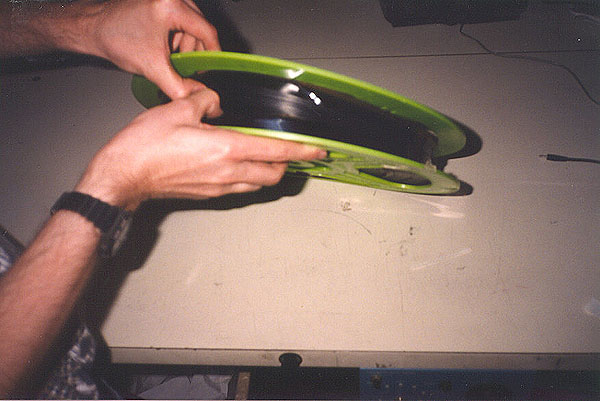
That would not have happened if the changeover theater that did this had at minimum a takeup failsafe in place (the kind with arms that drop down, not an optical presence sensor).
I used Pennywise's CA21 automations for many years and they made a changeover version of them that I used in my prior screening room. In the last 8-9 years when digital came around we contracted with them to build FT21 automation hardware for us (they use the same chassis as a CA21, but have infinitely more capability and I do all of the programming). As a result I just took a pair of those for my current screening room and wrote customized software from the ground up for running film.
Without getting into the various unique things this system does, the big thing I did differently that is applicable in this discussion is the addition of what I call a "delay bracket" on top of the machines. You can see the setup here...
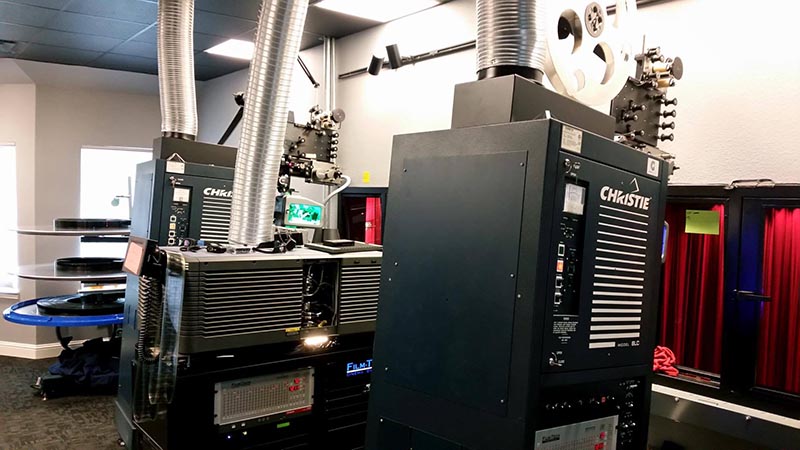
The idea is the cue detector that works for handling changeovers is positioned up TOP of the machine immediately after the film cleaner at the start of the delay bracket. (To generalize, essentially the delay bracket zig zags the film around half a dozen rollers that ends up putting 8 seconds of film in between the cue sensor and the projector gate.)
To prep a film for automated changeovers, I only need to place a cue 4 frames BEFORE the first frame I want shown on screen and 4 frames AFTER the last frame I want shown on screen. (The automation handles the various frame-precise delays internally to make the process of cue'ing prints ridiculously simple.) This way no frame counter is needed (so no unnecessarily handling) and cues are placed on the leaders and not on the actual projected stretch of film. The cue itself is also tiny and on the edge of the film that comes off quite easily.
The reason this design is so important is that MOST automated systems tend to use obnoxious cues that interfere with the picture or sound, and to make matters worse, most of them do not remove easily or cleanly. I'm sure everyone here has grumbled a few choice words over the years when they received a print like that.
When threading, I simply thread up at the start of the leader and then press a button on the automation where the projector will slowly run down to the exact start frame and stop, waiting to start at the changeover.
As a result of this, changeovers ALWAYS present every single frame, which is something simply not possible from a human operator. I also don't have to waste time worrying about how many frames there are after the final cue mark, if there are any splices between the two cue marks (or if they were scribed the correct distance apart to begin with), critical dialogue right up to the end of the reel, etc. In fact on-screen cues aren't even needed. The system will simply present every frame, every show.
And yes there are various sensors to monitor things and lots of other upgrades and neat things the system does, but even in a booth running 20 minute reels with a projectionist on duty 100% of the time, this type of system is ideal. All the projectionist has to do is make sure the next reel is threaded before the current reel runs out, but let the actual changeovers be done precisely by the system. Once the changeover happens, the projectionist simply goes to the projector that just finished running a reel and load up the next reel and press that button to cue itself up. In this sort of case, automation IMPROVES the show as well as the care of the print by eliminating the unnecessarily handling.
| IP: Logged
|
|
|
|
|
|
|
|
|
|
|
All times are Central (GMT -6:00)
|
|
Powered by Infopop Corporation
UBB.classicTM
6.3.1.2
The Film-Tech Forums are designed for various members related to the cinema industry to express their opinions, viewpoints and testimonials on various products, services and events based upon speculation, personal knowledge and factual information through use, therefore all views represented here allow no liability upon the publishers of this web site and the owners of said views assume no liability for any ill will resulting from these postings. The posts made here are for educational as well as entertainment purposes and as such anyone viewing this portion of the website must accept these views as statements of the author of that opinion
and agrees to release the authors from any and all liability.
|