|
This topic comprises 2 pages: 1 2
|
Author
|
Topic: Check Your Panastereo's! Battery Leakage!!!!!!
|
|
|
|
|
|
|
|
|
|
|
Randy Stankey
Film God
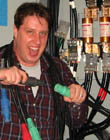
Posts: 6539
From: Erie, Pennsylvania
Registered: Jun 99
|
posted 12-24-2016 02:01 PM
What do you guys think about putting in some kind of battery holder instead of repeatedly soldering to the board?
The more times you reheat solder connections on a PCB, the more chance of failure. Repeated heating cycles weaken the intermetallic layer (the microscopic boundaries between components, solder and the copper traces on the board) and increases the chance of forming dendrites (solder whiskers) which can cause shorts or other failures.
By the time a consumer receives a piece of equipment, the PCBs inside might have already gone through three or more heating/cooling cycles at the factory. Double sided boards are heated twice in the reflow oven. Boards with transformers or heat sensitive components may have gone through a wave solder machine. Boards with special components might have to undergo selective soldering and/or hand soldering. That's four heats, right there! If there is rework or RMA, there could be five or more heats!
The guidelines that I am trained to work by say that two or three heats is the goal for maximum number of heating/cooling cycles. So, for instance, if I see a double-sided board with a defect on the first side I might hold it back and not send it to rework until the second side is built but that all depends on how many steps in the build process the board is supposed to have. It can get pretty complicated.
For instance, if a board has a BGA (Ball Grid Array) processor chip, we might have to send it to rework, right away. BGAs are more sensitive to reheating and, once they are soldered down, it is very difficult to rework them. You basically have one chance with a BGA. Through-hole components are more forgiving to reheating.
We get very specific work instructions as to whether a given board is Class-2 (Industrial/Mission-Critical) or Class-3. (Life-Support/Military) Once I get through my probationary period, I'm supposed to take classes for IPC Standard-610 which outline very specific workmanship standards. If you don't have your IPC-610 certificate, you can't do certain jobs in the place where I work. This is a big deal if you are working on a project, for instance, where the boards you make will go into the control systems on an F-16 fighter jet or something like that.
While this stuff might not be as important when you are talking about sound systems in movie theaters, I can tell you that, for some projects, we are as serious as a heart attack! There are certain boards, on certain projects that we aren't even allowed to touch with our bare hands.
Static-safe gloves. Anti-static wrist straps. Anti-static shoe straps. Must wear anti-static smocks at all times. When you enter or leave and re-enter the shop you have to stop at a check station to verify that you anti-static devices are working, even if you only go to the bathroom. If you don't, your name shows up on a display board for all to see. (You have to punch in your employee number each time.)
We're not allowed to have a pencil while on the work floor, even if it's only in your pocket. Ball point pens, grease pencils or Sharpie markers only. We're not even allowed to have ordinary paper on the shop floor unless it's inside an anti-static sleeve.
There is a blue line around the perimeter of the shop floor. If you step over that line and you're not following the rules, you can get sent off until you fix whatever problem you were caught for.
So... Long story short... I know that the boards in cinema processors aren't as critical as the ones that go in EKG machines or heart defibrillators but, if you want to keep your equipment working, this is something to think about. Especially if you're talking about vintage equipment that will be difficult or impossible to replace.
Overworking solder connections might cause a failure down the road.
It might be worthwhile to consider a no-solder solution if it is practical.
| IP: Logged
|
|
|
|
|
|
|
All times are Central (GMT -6:00)
|
This topic comprises 2 pages: 1 2
|
Powered by Infopop Corporation
UBB.classicTM
6.3.1.2
The Film-Tech Forums are designed for various members related to the cinema industry to express their opinions, viewpoints and testimonials on various products, services and events based upon speculation, personal knowledge and factual information through use, therefore all views represented here allow no liability upon the publishers of this web site and the owners of said views assume no liability for any ill will resulting from these postings. The posts made here are for educational as well as entertainment purposes and as such anyone viewing this portion of the website must accept these views as statements of the author of that opinion
and agrees to release the authors from any and all liability.
|