|
|
Author
|
Topic: Correct size of Vic 5 lower loop.
|
|
|
|
|
|
|
|
|
Simon Wyss
Film Handler
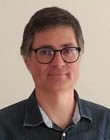
Posts: 80
From: Basel, BS, Switzerland
Registered: Apr 2011
|
posted 12-01-2016 04:44 AM
Interesting answers and I think Leo grasps it closest.
As a professional projectionist responsible to my employer (if not entrepreneur myself), the producer, and the audience I want to be able to guarantee synchronism in one of the seating rows of the hall. We used to call it the pistol row because there you would have perfect synch impression of pistol shots seen mid-screen with an American framing, wich is actors cut off above knee.
The standards provide 20 frames spacing between the optical axis and sound pick-up while the sound advance on prints is specified 21 frames ± a half. With the original head leaders one would find a 1000-Hertz beep of one frame length on the sound track corresponding to two seconds before content. Upon verifying one would count exactly 84 hole pairs, one or two more or one or two less. Everything else is out of standard and rejectable.
For correct reproduction I need to know the actual sound advance of each roll of a print. With this information I can scribble a cue note that I paste to the front wall between the projectors. Then I thread up each roll according to the print’s advances. The AMPAS technicians underlied a 100-foot throw theater with about 90 feet of hall length. The one frame difference between sound displacement on the print and the distance with the projectors causes dead synchronism at 1/24th of a second of sound travel in air at 20 degrees Celsius, which is 343 meters per second, thus 14,3 meters from the speakers.
Assuming at least one foot of distance between the screen and the speaker membranes behind it I care for a seat row at 14 meters away from the screen. Spectators closer and farther from the speakers will still have an acceptable impression of the show, although not strictly perfect. The discussion is perhaps ridiculous but at the same time about 85 years old.
| IP: Logged
|
|
|
|
|
|
|
All times are Central (GMT -6:00)
|
|
Powered by Infopop Corporation
UBB.classicTM
6.3.1.2
The Film-Tech Forums are designed for various members related to the cinema industry to express their opinions, viewpoints and testimonials on various products, services and events based upon speculation, personal knowledge and factual information through use, therefore all views represented here allow no liability upon the publishers of this web site and the owners of said views assume no liability for any ill will resulting from these postings. The posts made here are for educational as well as entertainment purposes and as such anyone viewing this portion of the website must accept these views as statements of the author of that opinion
and agrees to release the authors from any and all liability.
|