|
This topic comprises 2 pages: 1 2
|
Author
|
Topic: Christie P-35 Rotary Douser Installation
|
|
|
|
|
Tristan Lane
Master Film Handler
Posts: 444
From: Nampa, Idaho
Registered: Feb 2002
|
posted 07-25-2007 10:59 PM
quote: Mark Gulbrandsen I pity the tech that has a rivited in place front on his console! The front HAS to be removed to get at some of the Phillips Head screws holding the framing covers in place along the rear.
I've done a lot of these conversions, and on the P35GPS projector where hex head screws were used, a ball head wrench will just barely work the screw out. You may flex the snood a little bit in the process, but it will work. I only removed front panel on the first one I did. My thoughts are, of you are going to end up drilling out all the rivets, you might as well just drill one access hole in the snood lip instead to get access to that one screw.
I'd assume that the old projectors with the phillips screws will require the removal of the front panel, but as far as I know, the majority of SLC consoles have screws on the front panels, and the newer SLC consoles have screws securing the snood.
It is a PITA on the older stuff, but the benefits of the new douser will save countless hours of labor in the future maintaining the original c/o dousers.
And I agree, the ceramic piece makes the douser pretty much impervious to heat.
| IP: Logged
|
|
|
|
|
|
Mark Gulbrandsen
Resident Trollmaster
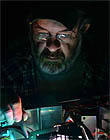
Posts: 16657
From: Music City
Registered: Jun 99
|
posted 07-26-2007 09:08 AM
Brad,
quote: Brad Miller It's called opaque black leader, Mark. You have the lamp strike on the black leader and then set up your cueing system from there, whether it be 8 seconds later or a minute via a start cue. Removing the douser takes that aspect of failure completely out of the chain. They simply are not needed on platter installations.
Well, the cue for me is having to set up the cues. Thats not going to happen with booth monkeys so try again...
You need to work in the real world for a while... where you have 700 customers with 500 dfferent ideas of how it should be done and ultimately 300 booth monkeys operating... most of em new! Its fun, its challenging, and you make a ton of money. The C/O is a tool that no one needs even know is there and it works without cue tape. Ultimately its the customers decision how its done and they are always right ya know.
quote: Tristan Lane I'd assume that the old projectors with the phillips screws will require the removal of the front panel, but as far as I know, the majority of SLC consoles have screws on the front panels, and the newer SLC consoles have screws securing the snood.
If they weren't so dam tight a right angle screw driver would be possible... but they're too tight. Removing the front cover isn't a real big deal an on SLC. The people likely to have problems would be those that have CH consoles or Strong. Most of those are rivited in place. I have P-35GP's that go back to when they first came out and some P-35C's that had the goofy idler for the intermittent drive that I converted over to the GP model (the factory said it couldn't be done...ha, in reality it takes less than 3 hours to do.)
Mark
| IP: Logged
|
|
|
|
Thomas Pitt
Master Film Handler
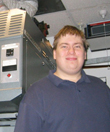
Posts: 266
From: Leeds, West Yorkshire, UK
Registered: May 2007
|
posted 07-27-2007 03:10 AM
What usually happens in Vue Leeds Light is the projectionist (or timer) starts the show; and the douser opens at that time. As soon as the film is up to speed, the lamp strikes. If they've put the film in the right place, the lamp should strike just as the first advert is about to start, so none of the leader is projected.
Often the lamp doesn't strike immediately, so you get the sound from the advert shortly before the picture appears. At the end of a showing, however, it's a little different. The final cue closes the douser, resets the lens turret and masking to flat (if it was a scope feature), puts lights up, and switches the sound back to non-sync. The film then tails out through the projector, but the lamp doesn't switch off until it has gone out of the projector completely. Is there any reason for this?
In Vue Sheffield, on the other hand, the lamp strikes as soon as the start button is pressed. When the film is up to speed and the lights have gone down, the douser opens to display the first advert. For some reason, this causes a tiny glitch in the non-sync sound - it briefly cuts off, then comes back on and fades down slowly, before switching over to the film sound.
| IP: Logged
|
|
|
|
|
All times are Central (GMT -6:00)
|
This topic comprises 2 pages: 1 2
|
Powered by Infopop Corporation
UBB.classicTM
6.3.1.2
The Film-Tech Forums are designed for various members related to the cinema industry to express their opinions, viewpoints and testimonials on various products, services and events based upon speculation, personal knowledge and factual information through use, therefore all views represented here allow no liability upon the publishers of this web site and the owners of said views assume no liability for any ill will resulting from these postings. The posts made here are for educational as well as entertainment purposes and as such anyone viewing this portion of the website must accept these views as statements of the author of that opinion
and agrees to release the authors from any and all liability.
|