|
This topic comprises 4 pages: 1 2 3 4
|
Author
|
Topic: The "perfect" threading procedure
|
Monte L Fullmer
Film God
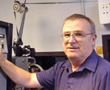
Posts: 8367
From: Nampa, Idaho, USA
Registered: Nov 2004
|
posted 02-19-2006 02:35 AM
Okey - time for another "show and tell" and this is is simply for what its worth:
We all know (or supposed to know) that distance between picture and sound is 21 frames with the sound ahead of the picture.
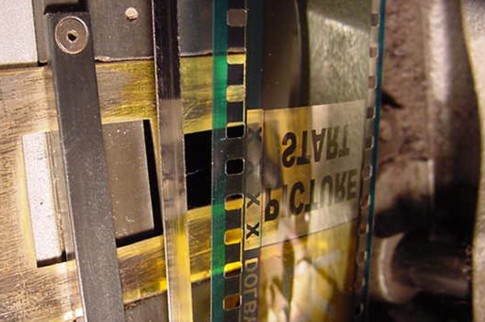
..and the sound blip almost straight across from the LED assembly:
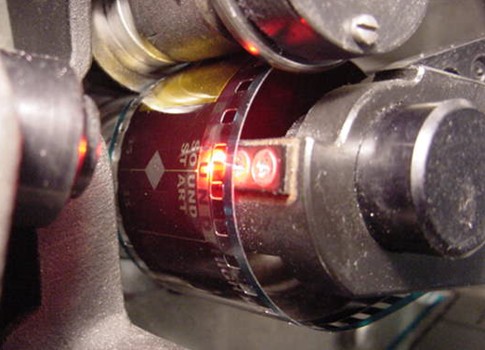
With these frames in their correct position, this becomes the "perfect" loop size for every machine that is out there.
Now, this is just for the well-known SIMPLEX XL/35 beauty that we either love or hate to death. In any case, we're stuck with this machine that has been with us since 1950. So, we'd better make the best of it.
When the frames mentioned above are in their right places, the loops become the 'perfect' size, as thus:
The Upper Loop -
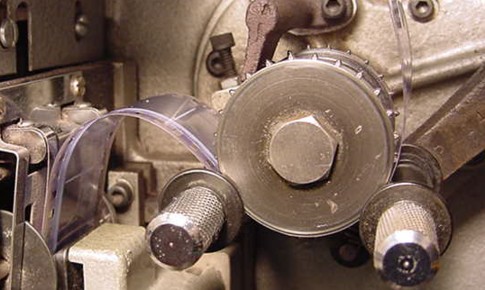
Now, I'm going to stop right here and explain something to you locations that have the curved gate variety:
1- Notice that the loop is entering the trap and gate assembly in FRONT of the band - not above the band.
With the film entering like this, the film, being made of our favorite abrasive material called 'polyester', there is less wear on the band since the film is parallel with the band on entry. If the loop is too big, the loop of film is ABOVE the band and contacting that upper round corner of the band. When the loop is like this, this oversized loop is putting massive wear on the top corner of the band wearing it down like nobody's business (anyone here had a band snap during a performance due to this...it ain't fun.. )
The Lower Loop:
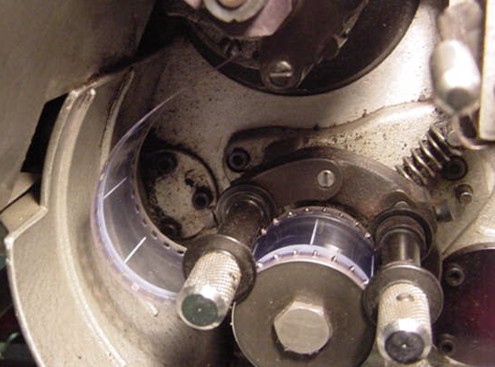
Now, heres's were I'm going to get some argument from quite a few here: I'm sure that a great deal of us have been trained that the lower loop is to be where the back side of the loop is a finger's width from the film to the back compartment.
Really, nothing wrong with that, but...how many of us love sports, especially the individual sports like golf, tennis, racquetball - anything that we have to it a ball with a device. Now, we know that with this form of sport, that if the ball is hit in a certain area of the device, the ball is hit true and the player doesn't even feel the hit after the followthrough...this is commonly called "the sweet spot"
..projectors have "sweet spots" as well and that is the 'correct loop size'. You make the loop size just right, the machine will run so much quieter to the point of the platter will be the one that one hears more than the machine. If one can hear the platter over the projector, then the lace job was a good one.
Thus, with the loop size only being a quarter-inch from the back wall, the film is leaving the intermittent sprocket in a straight line-not bending down and being a bit stressed as well.
In the picture above, there is a trick to do this every time one laces a machine: Notice where the frame line over the middle constant sprocket compared to the loop size. The frame line is almost at the 12:00 o' clock position. (I use that metal dowel spot, which is inbetween the two pad rollers on the pad arm assembly as my center point for the lower loop set) How we achieve this position of frame line and loop is to set the intermittent sprocket JUST AS THE SPROCKET has FINISHED TURNING.
We all know, when the intermittent sprocket has finished turning, the lower loop is at its largest size. The same with the upper loop - loop at the smallest size, AND the trick to this upper loop size is just the opposite in the pict below:
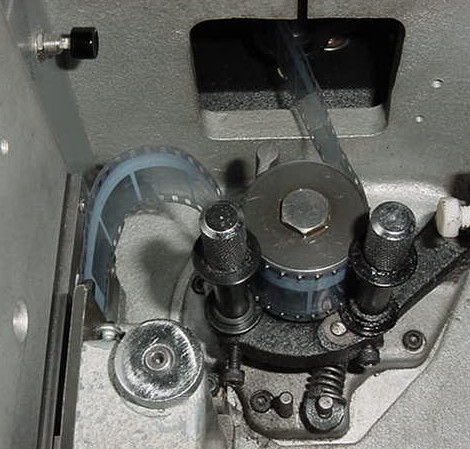
You notice that the frameline is at the 6:00 o' clock position. AND ... this pict is from the flat gate variety.
Important thing about flat gate Simplexes: that upper loop had better be as big as what's shown in the pict due to the fact that the rail top ends that stick up in the gate assembly DO NOT like small loops. You build a small loop, the splices will pop and snap as they head down into the trap assembly. These assemblies love to bust splices, especially weak ones if the loop is too small. AND, if the loop collapses, it will shear off the teeth from that driven fibre gear due to the sprocket will suddenly be pulled foward by the film when the loop is either too small or collapses. And those rail ends act like a fulcrum for the film to pull suddenly when the loop is too small and jerk on the sprocket, and shredding the teeth off that gear.
Thus, the trick is to have the loop tall enough so the film is heading straight down, after leaving the loop, into the trap without any bending or looping whatsoever. One could build the loop to where it about a quarter inch taller than the sprocket with the frame line at the 6:00 position - with the intermittent sprocket being stopped right after it gets into the locked position.
In short, if you would like to have a much quieter booth, try this out for size. It's amazing that the 6 plex that I work at, the machinery runs so smooth and with a steady 'purr' from these 1050's if laced up this way.
Anywho....for what it's worth to all.
And I'm sure that this technique is for all brands of machinery, for this is the only brand that I have available to demostrate this technique.
thx - Monte
| IP: Logged
|
|
|
|
|
|
|
|
|
|
Monte L Fullmer
Film God
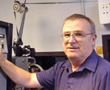
Posts: 8367
From: Nampa, Idaho, USA
Registered: Nov 2004
|
posted 02-19-2006 01:38 PM
Scott, I know that you disagree, at least, give it a try with my bottom loop size...you might just be suprised. If you don't like it, it's your choice, of course. quote: Scott Norwood Should one compensate by making the loop smaller?
..the Milleniums, with this raised upper sprocket, has the huge disadvange of wearing off the tops of the bands, when the loop was made the "normal" size, very horribly since that sprocket, being raised wasn't moved forward in the same distance as well so the loop size could be kept at the same ratio.
Thus, I do my best to maintain a much shorter loop so the film still woundn't be wearing on that corner of the band.. and it can be done with no qualms about having a upper loop too short.
Remember even with the machine running that the loops are only going up and down in a quarter inch span (with the simplex.. - as for other machines, in which I would love to try this out on century's and the P-35 Christies, in which I made those lower loops one sprocket after they touch that roller on that middle sprocket assembly...) so there really isn't that much worry of scratching unless one builds gigantic loops for some dumb reason.
Granted, the 21 frame count is at the speaker on stage. I believe that a one to two frame advance shouldn't affect the diagrams above due to the slack that is already there below the projector...and since this variable of film length to the soundhead is AFTER the middle sprocket, thus the above demostration that I posted can still be used.
Yes, the Supers and the E-7's - get that loop up there since these machines had that 'shute' assembly under the sprocket to make sure that the upper loop was tall enough, but not to hit the firetrap sensor, especially if an out of frame was encountered..
Thomas - on your V4e - there can be a simple way to figure this out and that is: take a leader with these markings, put the "picture start" in the trap, and go ahead and lace up the machine WITHOUT making your loop after the intermittent sprocket. Thread the machine as normal and when just before securing the film over that last sprocket, back the film up til the sound blip is in the designated area. I bet that the frameline will be at the 12:00 position on that last sprocket. Lock the roller down and then see if your lower loop, when pulling the film back is the correct size.
Then, for the upper loop, do the same with the frameline at the 6:00 position. See how this turns out, for this is the way I always threaded any Cine V(x) machine - where the 4E's and the majority of the V5's were the flat trap variety.
-thx a bunch, all ... - Monte
| IP: Logged
|
|
|
|
|
|
|
|
All times are Central (GMT -6:00)
|
This topic comprises 4 pages: 1 2 3 4
|
Powered by Infopop Corporation
UBB.classicTM
6.3.1.2
The Film-Tech Forums are designed for various members related to the cinema industry to express their opinions, viewpoints and testimonials on various products, services and events based upon speculation, personal knowledge and factual information through use, therefore all views represented here allow no liability upon the publishers of this web site and the owners of said views assume no liability for any ill will resulting from these postings. The posts made here are for educational as well as entertainment purposes and as such anyone viewing this portion of the website must accept these views as statements of the author of that opinion
and agrees to release the authors from any and all liability.
|