|
This topic comprises 2 pages: 1 2
|
Author
|
Topic: How do Cyan tracks save resources?
|
|
|
|
|
John Pytlak
Film God
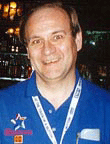
Posts: 9987
From: Rochester, NY 14650-1922
Registered: Jan 2000
|
posted 11-29-2005 09:03 AM
The details of the relatively complex procedure of "soundtrack application" are in the Kodak H-24 processing manual:
Kodak H-24.02 Processing Equipment
quote: Sound Track Processing Equipment The procedures for sound track processing on EASTMAN Color Print Film, are described in Module 9, Process ECP-2D Specifications. A close-up of the required equipment is shown in Figure 9-6. Because sound track processing is a precision operation, the required equipment must be kept in top operating condition. Alignment Maintain the venturi air squeegees in alignment, and the gaps specifications. To keep the applicated sound developer in the sound track area of the film, maintain the proper alignment between the guide rollers and backup roller relative to the applicator wheel. Also maintain alignment in the idler roller assembly to eliminate vibration and film twists. Keep the spray jets and squeegees aligned in the wash box to prevent contamination of the picture area with sound track developer. Align the sound-track application detector, if used. Check the alignment of the application equipment each time the processing machine is prepared for sound track development. Check the gaps between the backup roller and the applicator wheel during normal machine maintenance.
Kodak H-24.09 ECP-2D Process Specifications
quote: OPTICAL SOUND PROCESSING Overview The sound track is printed onto KODAK VISION Color Print Film / 2383, KODAK VISION Premier Color Print Film / 2393 and KODAK VISION Color Teleprint Film / 2395 / 3395 from a negative sound original. Only the top two emulsion layers should be exposed. This can be accomplished by using a filter pack comprised of KODAK WRATTEN Gelatin Filter No. 2B* and No. 12 in the light beam. In Process ECP-2D, the developer produces a positive silver and dye image of the sound track. The first fixer removes undeveloped silver halide from the sound track area. Next the bleach converts the silver sound track image back into silver halide. A sound developer is inserted between the bleach wash, which should be a 40-second deeptank wash, and the second fixer. This fogging developer reduces the silver halide in the sound track to a positive silver image once again. The silver and dye sound track image is not appreciably affected by the remaining processing steps.
(Read pages 9-32 to 9-37 to get an appreciation for the complexity of the added steps and the QC issues involved)
As you can see, lots of issues just to put that narrow band of silver on each print to make them compatible with old tungsten exciter lamps. Plus, if the prints are not properly recycled, that silver (a "heavy metal") ends up in fly-ash or a landfill. With over 10 BILLION feet of color prints made every year, the environmental impact is significant.
| IP: Logged
|
|
|
John Pytlak
Film God
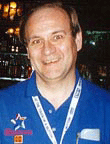
Posts: 9987
From: Rochester, NY 14650-1922
Registered: Jan 2000
|
posted 11-29-2005 02:16 PM
quote: Peter Mork (Film is produced and coated in massive sheets which are slit to width and then perforated - I reckon trying to do it your way would have its own set of problems, and cost a bundle.)
Yes, Kodak coats ("sensitizes") the film as wide rolls, about 54 inches across and well over 10,000 feet long. The rolls are then slit to 38 35mm strips, and then perforated. The emulsion properties are the same across the entire width of the roll, so you cannot make film with a different emulsion in the soundtrack area.
For a silver+dye soundtrack, the lab uses the special "soundtrack application" equipment, chemicals and procedures outlined in the Kodak processing manual:
1. Viscous caustic soundtrack developer containing hydroquinone 2. An extra fixer solution before the bleach ("First Fix") 3. Partial drying after the bleach wash 4. Precise application to only the analog soundtrack area, done on wet film moving at many hundreds of feet per minute 5. LOTS of fresh water to wash the developer off without splashing back into the picture area, causing stains 6. Extra QC to be sure the sound application has no defects
A red LED is efficiently modulated by cyan dye, and requires no silver in the track.
Old tungsten light readers have lots of IR sensitivity, that requires silver to effectively modulate
| IP: Logged
|
|
|
Stephen Furley
Film God
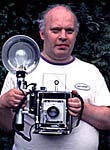
Posts: 3059
From: Coulsdon, Croydon, England
Registered: May 2002
|
posted 11-29-2005 04:20 PM
Using the standard colour print stock a dye track of any colour could be produced, depending on which layers were exposed. The reasons for not using the yellow layer have been discussed here previously, but why use the cyan layer? Why not the magenta layer with a green light? I assume that the cyan layer must have some advantage over the magenta one; or is it that red light sources have some advantage over green ones.
CDS used the magenta layer, but I think the reader used white light; I assume with a green filter in the path someware. Or was the ccd reader only green-sensitive?
Why not remove the silver, but still use both cyan and magenta dyes, as in a conventional track? This could still be read with a red light, or come to that, a green one. Is it that a sharper image is produced by using just one layer?
Anybody who is old enough, like myself, to have worked with the C22 Kodacolor process, and E2/E3 Ektachrome, will appreciate how much colour processes have been simplfied in the last 35 years or so. (C41 really has been with us a long time now, hasn't it? I was still at school when Kodacolor II was introduced.) To be honest, I'm rather surprised that the silver re-development process wasn't eliminated long ago.
| IP: Logged
|
|
|
|
|
|
|
|
|
All times are Central (GMT -6:00)
|
This topic comprises 2 pages: 1 2
|
Powered by Infopop Corporation
UBB.classicTM
6.3.1.2
The Film-Tech Forums are designed for various members related to the cinema industry to express their opinions, viewpoints and testimonials on various products, services and events based upon speculation, personal knowledge and factual information through use, therefore all views represented here allow no liability upon the publishers of this web site and the owners of said views assume no liability for any ill will resulting from these postings. The posts made here are for educational as well as entertainment purposes and as such anyone viewing this portion of the website must accept these views as statements of the author of that opinion
and agrees to release the authors from any and all liability.
|