|
This topic comprises 2 pages: 1 2
|
Author
|
Topic: Kinoton Platter Discussion (follow-up to 'Harry Potter Quality?')
|
Michael Barry
Jedi Master Film Handler
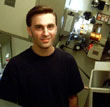
Posts: 584
From: Sydney, NSW, Australia
Registered: Nov 1999
|
posted 06-12-2004 10:32 AM
Continuing on from the discussion about Kinoton platters...
I'm going to respond to some points Brad made about them:
'Needs a platter mount film cleaner bracket no higher than 4 feet off the floor. Big Sky and MiT mount theirs at the top of the tree, apparently because they think everyone using their equipment is at least 9 1/2 feet tall. It needs to be somewhere around waist level for ease of use.'
At our theatre, we tapped into the column just above the top deck. I found this to be convenient and within easy reach (if you can operate the top platter, you can easily get to the Kelmar unit mounted just above it). I guess you can't mount it any lower because the Kinoton's payout path simply goes up and out, rather than all the way down, then all the way up and out (a la Speco, et al). Above the top plate does the job, however.
'True swivel rollers for feed and return, not the way Kinoton designed it with the feed one having 180 degrees of travel and the takeup one having the *other* 180 degrees of travel. That's stupid and accomplishes nothing, because the projector STILL has to be at that exact 90 degree angle to the platter!'
It is possible to place the platter where you want with the use of additional rollers. I *think* I remember one installation with the platter placed behind the projector and slightly off to one side. I can't remember how it was done; with additional rollers or perhaps the final payout roller was angled specifically to accomodate. I can't really imagine a placement scheme that couldn't be accomodated, though (as with any platter).
'Each platter should payout and takeup individually. If I have two ST-200 platters and I want to feed from one and takeup on the other, I should be able to do that! (I have not verified that this is indeed an issue, but was told that it was.)'
It isn't an issue. If it was, then interlocks wouldn't be possible. Cinemas 3 & 4 at the Ritz cinema are back to back (flanked by their respective auditoria). John Wilson set this up so that in addition to regular interlocks, there was also the possibility of playing a film in 3, but taking up in 4 (so that long prints wouldn't have to be moved there for the next session. ie. ROTK in #3 at 3pm, and in #4 at 7pm, no print movement needed). This meant that at the 3pm session, platter 3 was only paying out, whereas platter 4 was paying out one print and taking up two at the same time! (Taking up two prints at the same time is only possible due to the unique take-up design of the Kinoton). There was also the possibility of criss-crossing so that payout of 3 goes to 4 and payout of 4 goes to 3 at the same time.
'Automation should not have to *tell* the platter when the projector is started. The platter should be able to figure this out on it's own like all others.'
I don't know what you mean by this...I was able to start and stop the projector at will and the platter would know what to do. The automation wasn't necessary at all - the platter is totally independent.
'The platter should also be smart enough to be able to leave 3 brains mounted at all times and figure out which platter is the payout via the sensors and which platter is the takeup by which arm has been pulled. Duh!'
This isn't an issue, either. Simply by threading the brain the platter knows that that's the payout, and by loading the take-up arm, that deck would take-up. There are no switches (unlike Speco) to 'tell' the platter at any rate. Now, although I have taken up two films on these platters at the same time, I have not tested paying out two films at once. I doubt it would have any issues doing this, though. I will try it sometime and report back here.
'User-adjustable ramp speeds on payout is also desired. I've never met an "auto adjusting" platter that I liked, and the Kinoton is no different. No two platter decks are alike in speed. If I want the platter to take 10 seconds to ramp from full stop to full on at the start of the show, I should be able to set that. Likewise if I wanted it to reach full speed in 1.5 seconds, I should be able to set that. (Obviously the more sluggish the better.)'
With the excellent 'no moving parts' brains, payout speed isn't user adjustable, but it always seems to payout at the RIGHT speed. And there is really only one right speed, which is that the film never even gets close to wrapping either direction. In fact the feed angle is dead accurate at all times - better than any swing arm/moving parts brain that I have EVER seen. You simply cannot brain wrap with these...it's impossible. Now if payout ramp-up speed is too fast, you'll throw the print of course. If it's too slow to ramp up, you will wrap the brain, even if it's only a partial wrap (it has to keep up with projector feed, after all. Maybe it's the projector ramp-up that should be adjustable, and the platter simply has to follow?). So that the film touches nothing on start-up, the only speed desirable is the correct speed. And the Kinoton chooses this ideal ramp-up speed every time so that no prints get thrown, ever, and no wrapping occurs, ever.
Of course, the greatest benefit of all is that Ian Price can stand on one.
| IP: Logged
|
|
Brad Miller
Administrator
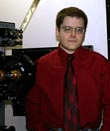
Posts: 17775
From: Plano, TX (36.2 miles NW of Rockwall)
Registered: May 99
|
posted 06-12-2004 12:08 PM
The thread referenced is here.
quote: Michael Barry 'Needs a platter mount film cleaner bracket no higher than 4 feet off the floor. Big Sky and MiT mount theirs at the top of the tree, apparently because they think everyone using their equipment is at least 9 1/2 feet tall. It needs to be somewhere around waist level for ease of use.'
At our theatre, we tapped into the column just above the top deck. I found this to be convenient and within easy reach (if you can operate the top platter, you can easily get to the Kelmar unit mounted just above it). I guess you can't mount it any lower because the Kinoton's payout path simply goes up and out, rather than all the way down, then all the way up and out (a la Speco, et al). Above the top plate does the job, however.
Maybe all Germans are 7 feet tall, but not every projectionist is. Having the cleaner that high is unacceptable. Besides, this leads to another gripe. The film needs to follow a common path (down, then up). No two decks should have a different payout (or takeup) threading path. Having a common roller at the bottom of the post provides this for payout. That is easily changed by Kinoton, but if they fixed all of my other gripes on the platter, I would be fine with the payout threading path as it is because I would simply drill new mounting holes for those payout rollers, thus fixing the design flaw in the field.
quote: Michael Barry 'True swivel rollers for feed and return, not the way Kinoton designed it with the feed one having 180 degrees of travel and the takeup one having the *other* 180 degrees of travel. That's stupid and accomplishes nothing, because the projector STILL has to be at that exact 90 degree angle to the platter!'
It is possible to place the platter where you want with the use of additional rollers. I *think* I remember one installation with the platter placed behind the projector and slightly off to one side. I can't remember how it was done; with additional rollers or perhaps the final payout roller was angled specifically to accomodate. I can't really imagine a placement scheme that couldn't be accomodated, though (as with any platter).
Additional rollers to do the job the platter should be able to do right out of the crate??? Unacceptable.
quote: Michael Barry 'Each platter should payout and takeup individually. If I have two ST-200 platters and I want to feed from one and takeup on the other, I should be able to do that! (I have not verified that this is indeed an issue, but was told that it was.)'
It isn't an issue. If it was, then interlocks wouldn't be possible. Cinemas 3 & 4 at the Ritz cinema are back to back (flanked by their respective auditoria). John Wilson set this up so that in addition to regular interlocks, there was also the possibility of playing a film in 3, but taking up in 4 (so that long prints wouldn't have to be moved there for the next session. ie. ROTK in #3 at 3pm, and in #4 at 7pm, no print movement needed). This meant that at the 3pm session, platter 3 was only paying out, whereas platter 4 was paying out one print and taking up two at the same time! (Taking up two prints at the same time is only possible due to the unique take-up design of the Kinoton). There was also the possibility of criss-crossing so that payout of 3 goes to 4 and payout of 4 goes to 3 at the same time.
There are many microswitch-based payout platters (Strong, Teco, etc) that rely on "seeing" the speed of the takeup for a reasonably smooth payout. When that is not present, it *can* payout, but much more rough. I want to insure that is not the case with the ST-200.
I wish I knew who told me this. Supposedly the payout derives some of it's logic from the takup speed. If this isn't an issue, that's great, but confirmation is needed that the takeup and payout are 100% seperate from each other and one doesn't "look" to see what the other is doing. Unfortunately I was unable to test this for myself due to the circumstances at the time.
quote: Michael Barry 'Automation should not have to *tell* the platter when the projector is started. The platter should be able to figure this out on it's own like all others.'
I don't know what you mean by this...I was able to start and stop the projector at will and the platter would know what to do. The automation wasn't necessary at all - the platter is totally independent.
I have been told this by at least 3 people who have installed them. There is apparently a hookup to the automation that tells the platter when to start. You were using automation, right? The platter should operate on demand of the film movement without any sort of command from the automation or external switch.
quote: Michael Barry 'The platter should also be smart enough to be able to leave 3 brains mounted at all times and figure out which platter is the payout via the sensors and which platter is the takeup by which arm has been pulled. Duh!'
This isn't an issue, either. Simply by threading the brain the platter knows that that's the payout, and by loading the take-up arm, that deck would take-up. There are no switches (unlike Speco) to 'tell' the platter at any rate. Now, although I have taken up two films on these platters at the same time, I have not tested paying out two films at once. I doubt it would have any issues doing this, though. I will try it sometime and report back here.
Again, that is not what I have been told. Supposedly if the brain is in the takeup platter, it will not function. Have you tried taking up a print on a deck that has a brain mounted? Please do so and report back.
quote: Michael Barry 'User-adjustable ramp speeds on payout is also desired. I've never met an "auto adjusting" platter that I liked, and the Kinoton is no different. No two platter decks are alike in speed. If I want the platter to take 10 seconds to ramp from full stop to full on at the start of the show, I should be able to set that. Likewise if I wanted it to reach full speed in 1.5 seconds, I should be able to set that. (Obviously the more sluggish the better.)'
With the excellent 'no moving parts' brains, payout speed isn't user adjustable, but it always seems to payout at the RIGHT speed. And there is really only one right speed, which is that the film never even gets close to wrapping either direction. In fact the feed angle is dead accurate at all times - better than any swing arm/moving parts brain that I have EVER seen. You simply cannot brain wrap with these...it's impossible. Now if payout ramp-up speed is too fast, you'll throw the print of course. If it's too slow to ramp up, you will wrap the brain, even if it's only a partial wrap (it has to keep up with projector feed, after all. Maybe it's the projector ramp-up that should be adjustable, and the platter simply has to follow?). So that the film touches nothing on start-up, the only speed desirable is the correct speed. And the Kinoton chooses this ideal ramp-up speed every time so that no prints get thrown, ever, and no wrapping occurs, ever.
I said "ramp speed", not payout speed, and I was not referring to the first 10 seconds when the platter starts spinning. I am referring to the ramp speed during the show. History has proven that anything "preset" is never optimized. As an example, Strong's SCDC platter is also preset and no two decks will ramp anywhere near the same speed. Some are jerky, some are smooth, some are too sluggish and drag the film around the brain. (Of course exact leveling is also unnecessarily important on those stupid things.) The Kinotons I watched were indeed exhibiting different payout behaviors. While none of them were bad enough to toss a print, it is still unacceptable that I can not adjust it the way I want it to behave. As a further example, I can adjust the inverter on a PK60 and tell it to take 10 seconds to get from 0-24FPS, or maybe I want 11.5 seconds, or perhaps 13.9 seconds. It is something that I can control to my liking. That is not present in any form on the ST-200. I should also be able to tell it absolute maximum speed, under any payout condition.
| IP: Logged
|
|
Michael Schaffer
"Where is the Boardwalk Hotel?"
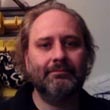
Posts: 4143
From: Boston, MA
Registered: Apr 2002
|
posted 06-12-2004 11:17 PM
The platters are connected to the projector so that the deck in which the brain is inserted starts spinning when the motor starts to give the film a smoother start. However, this is more of a bonus feature and not absolutely necessary. The brain alone is clever enough to keep the platter running at good regulated speeds.
Barry: to see if the platter pays out on 2 films simultaneously, you don`t need to set up 2 films. Just insert 2 brains, take bits of film and play around the photo sensors. In my locations back in Berlin (100% Kinoton), we used to do a lot of the things like you described, interlocking films across sveral screens, "depositing" the print on another platter deck, playing really big films over the interlock rollers to the platter deck where we worked for breakdown, so that we didn`t have to manually move the print.
BTW, I am not 7`, I am only 6`01``, but I never had any problems with reaching that far up to the film cleaner. Mostly because we didn`t have any. We rather kept the booth and equipment clean, never had any problems with dirt on the film, even after 6 months of Titanic. In part also because the Delrin gates are so smooth there is hardly any shedding and so easy to clean.
| IP: Logged
|
|
|
Steve Guttag
We forgot the crackers Gromit!!!
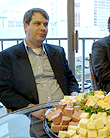
Posts: 12814
From: Annapolis, MD
Registered: Dec 1999
|
posted 06-13-2004 01:14 AM
Brad,
As to the payout speed...it has no relation to the take up speed from a control stand point. When the projector start, the payout is at the correct speed...even if the film is taking up in a different theatre.
As to Michael's comment about no need for the projector to tell the platter that it has started....I can absolutely state that the payout performance is unacceptable. Without the projector start command, the payout is in a "thread up mode" and is much more jerky since the speed has the dynamics of one threading up quickly.
As such I would say that if one is using theatre 12's platter to feed theatre 11 lets say (not an interlock situation) as a means of not having to physically move the film, there will be a more erratic payout.
While I can kinda understand how this would come up, I would say that I feel that the Kinoton payout spanks the Christie (and others) in its handling of film and as such would gladly accept that the projector tells the platter when it is running. Using simple switches one can have the projector running signal come from different theatres...heck even a rotary switch could allow a great number of theatres to control the platter. At the AFI/Siver, there is an ST-500E that can service either theatres 2 or 3 and both are normally changeover theatres. However with two toggle switches per theatre (one is for platter/changeover, the other is for projector 1/projector 2) the projectionist can have full platter bi-directional communication for start and film break.
As to the lack or poorly designed feed and take up rollers (The ones that are supposed to swivil) Kinoton just doesn't understand that their design is flawed. Also, the bottom platter should not have a unique takeup path...another flaw.
If you leave a payouthead in the platter for take up, the platter will function as a payout platter. Any unused platter with a payout head in it will start to spin upon projector start.
It would be a simple logic fix for those...if the take up arm is deflected, it is the take up platter...period...if no film is threaded in the payout head, don't spin.
Having worked with Christie AW1, AW2 and AW3s and now the Kinoton...for film handling...the Kinoton is easily the superior product...as to the logic and layout...Christie is better. I still like the Strong SCDC too...by far the fastest platter from crate to showing a film. Just plug it in and thread. Knock on wood, we've had zero failures with the SCDC and have been using them since their introduction.
Steve
| IP: Logged
|
|
|
Michael Barry
Jedi Master Film Handler
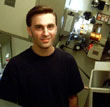
Posts: 584
From: Sydney, NSW, Australia
Registered: Nov 1999
|
posted 06-13-2004 09:04 AM
'I have been told this by at least 3 people who have installed them. There is apparently a hookup to the automation that tells the platter when to start. You were using automation, right? The platter should operate on demand of the film movement without any sort of command from the automation or external switch.'
Sorry - I took it literally when you said automation. There is definitely a hookup to the *projector*. When I started and stopped the projector manually, the automation was not involved at all. Our automation simply needed a 'projector start' command for projector motor/platter to begin transporting film. There was no need to send a separate command to the platter from the automation at the same time, so the projector/platter interface clearly did the rest. (It must, since there was no difference in performance if you manually or automatically started the projector).
The take-up paths for the lowest deck and the other two decks are different. However, I see this as an advantage as it enabled us to take up two prints at the same time onto the same platter. If the take-up paths were identical for all decks, this function would not be possible.
As to the platter not being able to take up with a brain inserted into the same deck, I will verify this. Come to think of it, I don't remember coming across this scenario before.
| IP: Logged
|
|
|
|
Brad Miller
Administrator
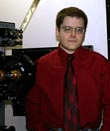
Posts: 17775
From: Plano, TX (36.2 miles NW of Rockwall)
Registered: May 99
|
posted 06-13-2004 03:49 PM
quote: Gordon McLeod I really don't have a problemwith a different threading path for the bottom deck since that is just part of the training proceedure. If an operator can't figure it out they shouldn't be there.
The same thing can be found on a Strong platter. While I agree with you the person in the booth should know how to properly thread up (among other requirements), I go into Strong booths ALL THE TIME and see someone taking up on the lower two decks running over BOTH of the rollers at the top of the tree... S C R A T C H ! ! ! ! ! It's a retarded design, and one that if Strong cared about would've been fixed a long time ago. That's why they are so lovingly referred to as Wrong International.
quote: Gordon McLeod The tie into the projector motor makes for probably the smoothest start up I have seen in any platter.
So? Big deal. I've never had ANY issues with a platter jerking upon startup, ever. Besides, if you are really that concerned about it, set the inverter in your Kinoton to ramp up at a rate of 15 seconds like I do. (and don't tell me you're not running Kinoton heads either)
quote: Gordon McLeod Since I always position any plater at a direct right angle to the projector the lack of swivel rollers is not an issue and again I tend to believe the guy who designed it new what he was doing so follow the instructions not re-engineer it
Contrary to German belief, the Germans are not right about everything. They can and do muck things up in their design from time to time. Having the platter at a 90 degree angle to the projector is the old school typical fashion, yes. But it's stupid. Most booths don't have a lot of extra space. By putting the tree square to the auditorium wall, you have effectively increased the amount of room the platter takes up from auditorium wall to back wall, where people must walk and move prints around in. Instead of 52 inches from one edge to the other, you now have 52 inches plus another 6-8 inches because of the tree. That is unacceptable in smaller booths. Besides, you're a fairly big guy. Having enough room to walk around the platter should be an obvious benefit to you, and whether you walk around or reach around the tree during threading, the option should be there for the projectionist to make that decision for themselves.
Turning the platter 45 degrees or so toward the projector aleviates all of this and for those concerned for whatever reason, it also lessens the amount of twist that the film is going through as well.
| IP: Logged
|
|
|
Brad Miller
Administrator
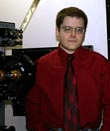
Posts: 17775
From: Plano, TX (36.2 miles NW of Rockwall)
Registered: May 99
|
posted 06-13-2004 06:44 PM
The "one side for all" is a little different than what I am used to, but it's something I can deal with. My biggest beef with it is that I prefer the platter to be on the operator side. I know that the typical theater puts them on the non-op side for fear that someone will walk into the film, but that's just never been an issue. Having the platter on the operator side cuts down on threading time and the projectionists don't tend to ignore it once it is threaded. They are far more likely to notice a platter problem on the operator side. That being said, having all of the threading path on the right side (facing the tree) makes that an unnecessary pain in the butt.
Regarding the takeup arm, I can deal with the film winding on the platter vertically, but much prefer it to enter horizontally and twist upright for the reasons Steve mentioned as well as dust issues. Not all booths are squeaky clean (actually I've never really seen one "squeaky clean") and as a result dust that settles on the deck between shows, during shows, overnight, etc will get scooped up onto the film moreso than a platter that has the film twist upright into position on the roll. This assumes of course there is a takeup adjustment like the AW3 has so the final roller can be adjusted as high as possible. On the average 2 hour film, the outer half of the decks won't ever even come into contact with the film that way.
Re: projector ramp up speeds...why not set the inverter to 7.0 seconds ramp up and just do a simple calculation as to what number to thread up on? From there a minor change (say 6.5 seconds) could be determined to get things so the cue frame falls on a "number".
| IP: Logged
|
|
Steve Guttag
We forgot the crackers Gromit!!!
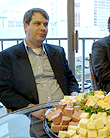
Posts: 12814
From: Annapolis, MD
Registered: Dec 1999
|
posted 06-13-2004 07:07 PM
RE: Ramp up....the sound head will not be up to speed and stable if one has the projector hit speed right when the douser opens.
With a 5-second ramp up, the soundhead has stabilized. One could argue about the need for 2 full seconds for stabilization but I haven't had a problem with 4-second ramp ups either. And for changeovers...I tend to go with under 3-seconds.
I tend to agree that I prefer that the platter be on the operating side of the projector if competent people are using it and Kinoton puts the rollers on the far side...the majority do place the platter on the non-stepped on film side so this is a benefit.
Most other platters require both side access for comfortable threading. For those theatres where the platter is shoe-horned against a wall (just a little cubby for the projector and platter) they are just a pain if one needs to get to the "other side".
Kinoton does offer the option of placing the platter behind the projector (behind the lamphouse)...that is about the easiest threading path in existance and if you don't have a back-to-back theatre or hallway space problems it is quite slick. The only question I have for Kinoton with this method is why they felt it necessary to place the exhaust stack centered on the film path. Offsetting the exhaust stack on their lamphouse would provide a light lock too as well as providing for a clean clear film path.
As to the Stong SCDC...I did say I have not had any problems with the ones I've installed...not that woorld wide they are problem free.
As to the AW3 versus SCDC installation time...no contest...the SCDC can be up and running as good as it is going as fast as you can get it out of the crate. The AW3 needs to be tweeked once assembled...get the return springs loosened up, the speeds set..etc.
As to the microswitch platter...once has to keep the deck speeds precisely balanced and the switches must be changed every 18-months. Most of the theatres I service that have microswitch or phase control centerfeeds, seem to almost never use the bottom platter even though I stress that they should distribute their usage amung the three decks. So, during the busy season when they are forced to use their off platter deck, wraps and such ensue. I don't have that with the SCDC and other independent speed systems (AW3s as well).
My most maintainance prone units are the AW3s and lower end Potts/Strong. AW3s seem to need their speeds set, have LED and photoresistor failures, drive tire failures (I'm on Wolk ones now...I can't tell you how many recalled Christie ones I've gone through) and my favorite...the wiring harness that burned up because the #1822 work lamp shorted out when someone smashed into it when removing the center ring. Why Christie never fused their power supply is beyond me...we generally do when we service one (Takes two fuses).
The Strong/Potts are a little more routine...change the speed setting device (microswitch/phase control), balance the speeds out and check the drive tires and replace if hardened or flattened (rount drive tires).
The SCDCs are near maintainance free though their drive tires should be checked as well. I don't have enough Kinoton's to evaluate their service issues. The other platter we service is the various SPECOs, mostly LP-270...they are also typically low maintainence.
Steve
| IP: Logged
|
|
|
|
|
All times are Central (GMT -6:00)
|
This topic comprises 2 pages: 1 2
|
Powered by Infopop Corporation
UBB.classicTM
6.3.1.2
The Film-Tech Forums are designed for various members related to the cinema industry to express their opinions, viewpoints and testimonials on various products, services and events based upon speculation, personal knowledge and factual information through use, therefore all views represented here allow no liability upon the publishers of this web site and the owners of said views assume no liability for any ill will resulting from these postings. The posts made here are for educational as well as entertainment purposes and as such anyone viewing this portion of the website must accept these views as statements of the author of that opinion
and agrees to release the authors from any and all liability.
|