|
|
Author
|
Topic: To brake or not to brake?
|
|
|
|
Bill Langfield
Master Film Handler
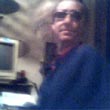
Posts: 280
From: Prospect, NSW, Australia
Registered: Apr 2001
|
posted 05-24-2001 10:31 AM
Mitchell,Clearly you need more experience. If you are breaking film, you need to get used to waiting for the join, then slowing the mut and plate at the same same time. Can you break down film on the rewind bench from 6000ft to flat bobbin cores. AND PACK ALL THREE SPOOLS TIGHT?? As Brad said, er, I don't know what Brad said However those brake switches/buttons are USELESS. The only way I see those brake butoons of use is for some one taking 3 hours to break down a 3 hour movie. Bill. Yes I know you should not make-up/break-up at more than the 2X projector speed, but that law went out when they started PRINTING at 10x, and with high speed Eprad Muts On the bench 2000ft to 2"core = 1.30secs. Thats a good rate reference for you.
| IP: Logged
|
|
|
Christopher Seo
Jedi Master Film Handler
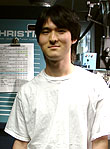
Posts: 530
From: Los Angeles, CA
Registered: Jun 99
|
posted 05-24-2001 02:28 PM
I never use the BRAKE feature. The key is never to let the film go slack. If it goes slack and then pulls tight again that is when an acetate break or polyester crinkling will occur. Always decelerate slowly while applying drag to the feeding end: when making up, lightly press the flanges of the reel on the MUT; when breaking down, lightly squeeze the edge of the platter deck. This should keep the film taut (of course you don't want to put too much tension on the film). You will have to vary this manual pressure depending on how quickly you decelerate and how close the film is to the center (tension naturally increases as you get closer to the center of a reel or platter). Note, if you leave the AW3 motor engaged when breaking down, this provides lots of tension so the film will probably stay taut without requiring manual drag (providing you still decelerate at a moderate pace). Also, before you start up again, gently pull the film tight on the feed end and apply a little drag as you start.Of course, there are still times when the film may go slack. While reaching over the AW3 MUT controls to adjust speed once, I brushed the switch from "LOAD SPINDLE" to "LOAD PLATTER" and then back again in panic. The film slackened and then pulled tight again very quickly (this was at high speed). Or the problem could be out of your control, such as a power outage. In my opinion, if the film should go slack for any reason, always turn the MUT off, and grab and completely stop the take-up end first. If you're breaking down at high speed, sure, some film will spill off the platter onto the floor, but it's better than the film pulling tight and snapping, and your floor should be decently clean anyway. Of course, under ideal situations such as home screening, you can go at a leisurely pace anyway.
| IP: Logged
|
|
|
|
Bill Langfield
Master Film Handler
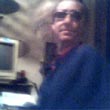
Posts: 280
From: Prospect, NSW, Australia
Registered: Apr 2001
|
posted 05-25-2001 11:55 AM
Mitchell, Sorry for the confusion...1:00.00 = 1hour 1.00 = 1 minute That proberly makes no sense. In any case I was saying you should be able to wind a 2000ft in 1 1/2 (90 secs) You said you dont have 6000ft spools, that's is pitty. So you are breaking down / making directly fom the bobbin cores?? Oh another safety tip, don't make up or break down at too hight speed on those plastic chri*** centre rings they can fly off) Bill.
| IP: Logged
|
|
|
|
|
All times are Central (GMT -6:00)
|
|
Powered by Infopop Corporation
UBB.classicTM
6.3.1.2
The Film-Tech Forums are designed for various members related to the cinema industry to express their opinions, viewpoints and testimonials on various products, services and events based upon speculation, personal knowledge and factual information through use, therefore all views represented here allow no liability upon the publishers of this web site and the owners of said views assume no liability for any ill will resulting from these postings. The posts made here are for educational as well as entertainment purposes and as such anyone viewing this portion of the website must accept these views as statements of the author of that opinion
and agrees to release the authors from any and all liability.
|