|
|
Author
|
Topic: Brad's "Dye Transfer" Review
|
Jeff Taylor
Jedi Master Film Handler
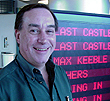
Posts: 601
From: Chatham, NJ/East Hampton, NY
Registered: Apr 2000
|
posted 03-12-2001 10:01 AM
I enjoyed Brad's review of the "new IB", and couldn't agree more. Just a minor point, though, for some of the guys who may not have experienced the original Dye Transfer process, or want to know more about it. The actual camera negatives were/are used to produce a high relief monochrome gelatin postive called a matrix (one for each color-YCM) which was then inked with the dyes more or less like a rubber stamp, and then moved along by a "pin belt" pressing the dye onto blank stock (in full daylight) with the silver soundtrack already in place. Each of the three colors was added sequentially. One of the beauties of the system, apart from the spectacular dense colors, is that the camera negatives are only used to produce one set of matrices which could generate several thousand prints if properly cleaned and reinked. Given todays fine grain duping stocks this is not so much of an issue, but in the old days it was a tremendous advantage as each print was more or less the quality of a contact print off the camera negative. If there are wrinkles in the new system that differ I apologize, but that's how IB was produced.
|
|
|
|
|
John Pytlak
Film God
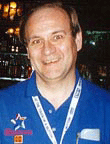
Posts: 9987
From: Rochester, NY 14650-1922
Registered: Jan 2000
|
posted 03-12-2001 11:18 AM
Jeff:Sorry, but you will have to ask Technicolor. Many of the details of the dye-transfer process are considered proprietary. Here is what their website says: __________________________________________ Improved Dye Transfer Process - Offering tremendous benefits to the film community, this process provides improvement for: Release Print Features Improved and increased color saturation Increased sharpness and reduced granularity Extended latitude with neutral tone scale (i.e. blacker blacks and whiter whites) Increased dark-keeping stability in image dyes (no fading) Process Features Greater creative control Increased consistency of release prints Compatibility with digital sound formats Compatibility with digital picture files ________________________________________ http://www.technicolor.com/aboutus/index.html ------------------ John P. Pytlak, Senior Technical Specialist Worldwide Technical Services, Entertainment Imaging Eastman Kodak Company Research Labs, Building 69, Room 7419 Rochester, New York, 14650-1922 USA Tel: 716-477-5325 Cell: 716-781-4036 Fax: 716-722-7243 E-Mail: john.pytlak@kodak.com Web site: http://www.kodak.com/go/motion
|
|
John Schulien
Expert Film Handler
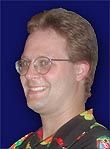
Posts: 206
From: Chicago, IL, USA
Registered: Nov 1999
|
posted 03-12-2001 12:38 PM
Some details of Technicolor's new dye transfer process may be proprietary, but they did take out a patent which reveals many of the details of their new printer. Extremely interesting reading. http://www.delphion.com/details?pn=US06002470__ Follow the link and select "View Images." if you're curious. In dye matrix printing, a matrix film is soaked in dye, then brought into contact with a receiver film. The film then migrates from the matrix into the receiver. The problem is that the dye migration process takes a fairly large amount of time -- some 40 seconds, which is a problem if you want to run a cine printer at high speed. The previous method involved using an extremely long stainless-steel pin-belt, which held the two strips of film in close alignment. The extremely long pin-belt was very difficult and expensive to maintain, and tended to wear out. The new method takes advantage of the fact that once the matrix film is pressed against the receiver film, the two tend to stick together. The new printer uses a relatively short pin-belt to align and stick the film together. The film is only on the pin-belt for a few seconds. Then, the matrix-receiver film sandwich is peeled off the pin-belt, and run through a series of rollers in a cabinet for the rest of the 40-second or so dye transfer time, and finally the sandwich is peeled apart at the end. Finally, the completed film is mounted on a broken plastic reel and delivered to the customer. (This detail is not included in the patent.) Interesting reading.
|
|
|
|
|
All times are Central (GMT -6:00)
|
|
Powered by Infopop Corporation
UBB.classicTM
6.3.1.2
The Film-Tech Forums are designed for various members related to the cinema industry to express their opinions, viewpoints and testimonials on various products, services and events based upon speculation, personal knowledge and factual information through use, therefore all views represented here allow no liability upon the publishers of this web site and the owners of said views assume no liability for any ill will resulting from these postings. The posts made here are for educational as well as entertainment purposes and as such anyone viewing this portion of the website must accept these views as statements of the author of that opinion
and agrees to release the authors from any and all liability.
|