|
|
Author
|
Topic: How to help prevent brainwraps on a speco platter system.
|
Darryl Spicer
Film God
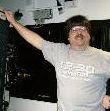
Posts: 3250
From: Lexington, KY, USA
Registered: Dec 2000
|
posted 01-03-2001 11:43 PM
Here is an idea for all of you out there who use speco platter systems. I have been doing this for the past two years and have greatly reduced my wraps.All you need is a full roll of splicing tape or one of the large trailer cores. Not the ones used for feature film cores or the tiny trailer cores. All you have to do is after you have started the film and the film is running up to speed is place the roll or core into the brain between the little black stopper and the control fingers so the fingers only open up so far. This will help prevent the film from being pulled in between the large roller and the control fingers during a static situation. It does not scratch anything and I have not had any problems with the platter running to slow. If anything I think the platter runs more smoothly. One note though, Do not use this method if you are interlocking because the takeup is not being used. one platter does not run full speed on a speco when the takeup is not being used. With the above method and the payout failsafes I installed a year and a half ago static brainwraps are almost a thing of the past at my theater.
| IP: Logged
|
|
|
Paul Konen
Jedi Master Film Handler
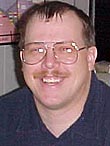
Posts: 981
From: Frisco, TX. (North of Dallas)
Registered: Jun 99
|
posted 01-04-2001 08:08 AM
Credit for this fix goes to Ethan Harper, fellow Film-Tech'r.Take a piece of masking tape and double it up to prevent any sticky from showing and make crimp marks about every 1/8 th inch or so. Attach it to the payout and the first roller to the right of the payout as if you are right in front of it. The crimping allows the arm to fully function and the tape helps prevent the double feeds associated with a wrap. This was a very helpful solution during our run of SW-EP1 as Film Guard was unavailable then.
| IP: Logged
|
|
Randy Stankey
Film God
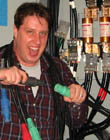
Posts: 6539
From: Erie, Pennsylvania
Registered: Jun 99
|
posted 01-04-2001 08:44 AM
My "home base" theatre here in Greensboro, NC has been pretty creative in the Anti-Brainwrap department....They have been using the roll of splicing tape in the payout arm trick for a while now. They have also come up with this little jewel to keep the film from double-feeding and getting caught up in the brain rollers... I thought it was a pretty cute idea.
| IP: Logged
|
|
|
|
|
|
John Pytlak
Film God
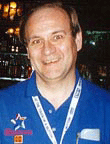
Posts: 9987
From: Rochester, NY 14650-1922
Registered: Jan 2000
|
posted 01-04-2001 09:49 AM
Good suggestions, all.  Even though Kodak VISION Color Print film has a conductive antistatic backing, the film must be in contact with a conductive surface so there is a path to ground for any static buildup. Non-conductive painted, plastic or anodized platters and rollers should be periodically treated with a topical conductive antistat like "Static Guard", "Endust for Electronics", "ACL Staticide", or other antistat used for clothing or electronics. AFAIK, Kelmar now sells a conductive "Platter Mat", similar in concept to the conductive floor mats used in electronics assembly areas to prevent buildup of static charge from "zapping" sensitive electronic components. Kinetronics, Meech and Simco sell static control equipment like conductive fiber brushes and antistatic ionizers. Maintaining the recommended 50-60 percent humidity in the projection room also helps reduce the static problems caused by dry winter heat. ------------------ John P. Pytlak, Senior Technical Specialist Worldwide Technical Services, Entertainment Imaging Eastman Kodak Company Research Labs, Building 69, Room 7419 Rochester, New York, 14650-1922 USA Tel: 716-477-5325 Cell: 716-781-4036 Fax: 716-722-7243 E-Mail: john.pytlak@kodak.com
| IP: Logged
|
|
|
All times are Central (GMT -6:00)
|
|
Powered by Infopop Corporation
UBB.classicTM
6.3.1.2
The Film-Tech Forums are designed for various members related to the cinema industry to express their opinions, viewpoints and testimonials on various products, services and events based upon speculation, personal knowledge and factual information through use, therefore all views represented here allow no liability upon the publishers of this web site and the owners of said views assume no liability for any ill will resulting from these postings. The posts made here are for educational as well as entertainment purposes and as such anyone viewing this portion of the website must accept these views as statements of the author of that opinion
and agrees to release the authors from any and all liability.
|