|
This topic comprises 4 pages: 1 2 3 4
|
Author
|
Topic: Carbon Arcs
|
Dave Bird
Jedi Master Film Handler
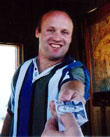
Posts: 777
From: Perth, Ontario, Canada
Registered: Jun 2000
|
posted 06-23-2000 09:50 AM
I hope I'm not bothering anyone, maybe you've all discussed this to death. What I find interesting, and especially with the talk about the drive-in recently that was switching to 3K Xenon, is that many of you seem to prefer the old arc lamps. One fellow recently mentioned that he wasn't sure whether a particularly great presentation he saw was the high quality of the print or not. This was the first time he'd seen a film lit with carbons, and thought that might be the reason for the "warmth" of the light. I completely understand the economics now, but as a "hobbyist", I'm curious as hell to spark up some carbon! My lamps were running 13.6mm, but you could buy kits for 11, 10, and even 9. Does anyone know what kind of amps/ output for the 9's and 10's? Or where I might find a chart? What are the comparitive light outputs between these old girls and Xenon? My manual only lists the two larger sizes. And hey, if anyone has any interesting stories, fire away!------------------ Dave Bird
| IP: Logged
|
|
|
|
John Walsh
Film God
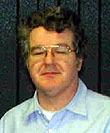
Posts: 2490
From: Connecticut, USA, Earth, Milky Way
Registered: Oct 1999
|
posted 06-23-2000 02:44 PM
Prints were color-timed for carbon arc for many years after xenon was in widespread use. I think they are being timed for xenon now.While I really do like the look of carbon arc, let me assure you it was a job to run them. You were always cleaning, tweeking, and cleaning some more. Ash in the lamphousing, on the reflector, up the stack; all of this had to be cleaned away (the fire police inspector would stick their hand way up the stack to check.) Silver polishing the carbon jaws, scraping the melted copper away (sometimes off of the reflector- be careful!), certain kinds of oil (regular, graphite, etc.) had to be used in certain places. The carbon feed speeds would vary during the day depending on the local line voltage, so you would have to check it. The booth would get hot. The carbon end would sometimes break off, so the light would look weird until a new crater got burned in (about 3-4 min.) The ability to guess at how long a stub would last varied from one operator to another- sometimes with a melted silver jaw as a result (an Ashcraft 13.5mm negative jaw cost $260 in 1978.) No, thank you.
| IP: Logged
|
|
Scott Norwood
Film God
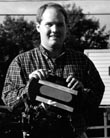
Posts: 8146
From: Boston, MA. USA (1774.21 miles northeast of Dallas)
Registered: Jun 99
|
posted 06-23-2000 03:02 PM
John's points are valid. I started a little more than two years ago in a single-screen with 6000' reels and xenons and have since been the fill-in guy at a single-screen with small reels and carbons and a 10-screen automated multiplex with platters, start timers, etc.
Of these three different arrangements, I'd say that the single-screen with carbons required the most actual work, but that the multiplex required the most knowledge (not only projectors, but also platters, automation systems, fancy sound systems, etc.). I've enjoyed all three environments, but for different reasons; all of them have been interesting experiences.
If I were building a new single-screen theatre or renovating an old one, though, I'd definitely go with 6000' reels (or at least the capability to run 6000' reels) and xenons. It would be pretty silly to install rebuilt carbon arc equipment today (except maybe for followspot use), although I agree that it does look beautiful onscreen.
| IP: Logged
|
|
Dave Bird
Jedi Master Film Handler
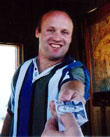
Posts: 777
From: Perth, Ontario, Canada
Registered: Jun 2000
|
posted 06-23-2000 03:25 PM
Agreed, I wouldn't install them either to run a "real" theatre. But my initial plan is to learn how to run these suckers (probably thrown to the side of my barn). I knew when I took these lamps that I really had little chance of ever lighting them, though I would've liked to, for the experience. And you gotta admit, for sheer "wow" appeal to patrons or folks who don't have to deal with them everyday, the carbons are pretty cool. That being said, my dream drive-in features 3 screens with completely modern booth upstairs, but for screen 1, an additional glass-enclosed (visible to patrons) old-time changeover-carbon setup for when the boss felt like stepping back in time. Neat idea? I think so. Realistic? Probably not, course building a drive-in probably isn't either. But I'm having fun with that equipment. Thanks guys.------------------ Dave Bird
| IP: Logged
|
|
|
|
|
|
|
|
|
|
Tim Reed
Better Projection Pays
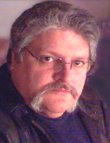
Posts: 5246
From: Northampton, PA
Registered: Sep 1999
|
posted 06-25-2000 09:17 AM
Lorraines were from France (Fronce!), and were imported by Carbons, Inc. UCAR made "Nationals".  I think they're ALL bulk-purchased from Lorraine now, anyway... even the Marble brand. Everyone just puts their individual stamps on. The ones I liked the best, Union Carbide, curtailed projector carbon manufacture years ago. Then, they would make a big run about once a year, to fill accumulated orders. Before long, even that was discontinued. Yes, carbon arc operation... I loved it! It was when the job was a CRAFT. ------------------ Better Projection Pays!
| IP: Logged
|
|
|
All times are Central (GMT -6:00)
|
This topic comprises 4 pages: 1 2 3 4
|
Powered by Infopop Corporation
UBB.classicTM
6.3.1.2
The Film-Tech Forums are designed for various members related to the cinema industry to express their opinions, viewpoints and testimonials on various products, services and events based upon speculation, personal knowledge and factual information through use, therefore all views represented here allow no liability upon the publishers of this web site and the owners of said views assume no liability for any ill will resulting from these postings. The posts made here are for educational as well as entertainment purposes and as such anyone viewing this portion of the website must accept these views as statements of the author of that opinion
and agrees to release the authors from any and all liability.
|